The Thistles Car Park - McConnell
Project
The Thistles Car Park
Product
Triflex Deckfloor RS Waterproofing wearing layers with Quartz or Emery
Size (M2)
1500m2
Contractor
McConnell
Winner
LRWA Awards 2025 - Highly Commended - Liquid Roofing Project of the Year
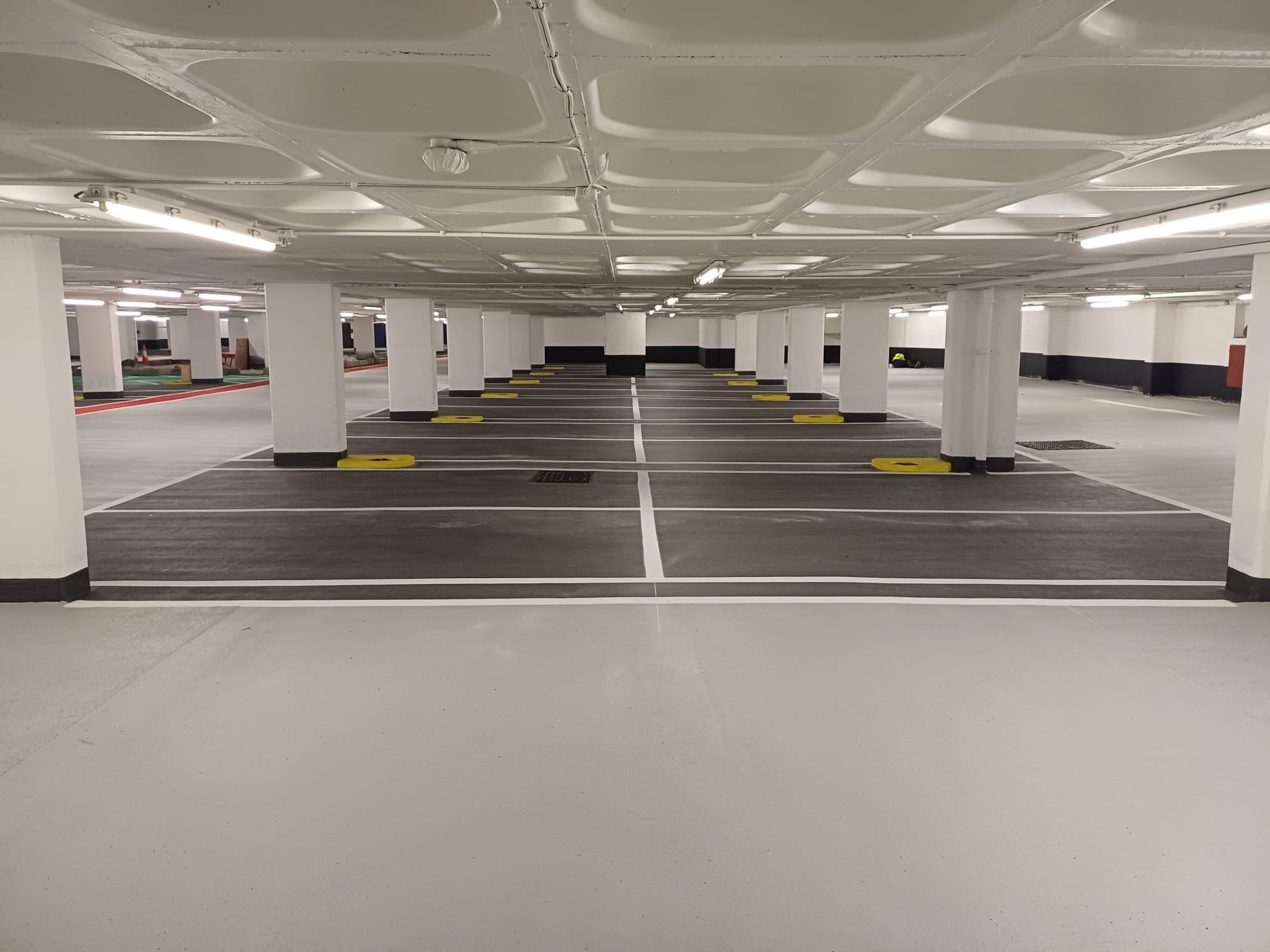
- The Background
The Thistles Shopping Centre is in Stirling, Scotland and covers over 500,000sqft of retail space providing 87 units since its opening in 1977. Based in the heart of Stirling it allows for a catchment of over 500,000 people and it is estimated that it has 12 million visitors per year. As part of ongoing improvement plans, the centre has also invested more than £3.5 million to bring the Thistles Car Park back into operational use.
The car park spans across six (6) levels and is constructed primarily in a reinforced concrete frame structure with reinforced concrete waffle pot floors/reinforced concrete beam construction and concrete cladding panels.
There are two separate car parks and since COVID, one side (named T2) remained closed and unoccupied. This enabled works to be completed without causing disruption to retail tenants or occupiers of the shopping centre, the closing any of the car park levels, or reducing spaces, or phasing the works and allowed for a continual approach and out of hours working.
The other side of The Thistles Centre Car Parks (T1) remained open, operational and very busy with traffic entering and leaving on a regular basis.
- The Challenge
The full scope of works consisted of resurfacing, redecoration, the introduction of energy efficient lighting, a new air extraction system and a new fire detection system. McConnell were appointed to undertake the resurfacing works which included addressing the issues of the concrete structure and failings of the existing waterproofing system via:
• Enclosed shot blasting
• Grinding and planing to remove all coatings, line markings, laitance, boss surfacing in preparation for repairs and new surface finishes
• Repairs to cracks
• Concrete repairs and infills
• Repairs to ramps
• Scrape, brush and removal of loose materials
• Degrease exposed metals with Triflex Cleaner
• Apply Triflex Metal Cleaner and Metal Primar to exposed metals
• Apply Sika Monotop Primer to concrete repair areas
• Apply Sika Monotop to concrete repair areas
• Apply Triflex Deckfloor Primer
• Apply Triflex Deckfloor RS Waterproof Wearing Layer with Quartz
• Apply Triflex RS Waterproof Wearing Layer with Emery
• Apply white lining
• Install directional signage
• Additional decoration works to ceilings, walls and columns and staircases between floors.
- The Solution
A BESPOKE SOLUTION BACKED BY SCIENCE
Working with Triflex authorised contractor McConnell’s, the Triflex technical team undertook a detailed survey to establish the current state of the car park, confirm general condition and undertake a range of tests to identify the best solution.
Multiple core tests were taken to establish exactly the varying conditions of the car park deck at every level. Adhesion tests were also carried out in-situ on the existing concrete deck to confirm any pre-treatment or primer requirement.
The car park condition was confirmed to consist of concrete deck to all levels with a migrating corrosion inhibitor and waterproofing coating layer which on levels 1 and 2 had delaminated and since largely been removed.
The coatings to Level 3 and 4 mostly remained although there was extensive delamination in these areas. The reason for this coating delamination is unclear, but possibly resulting from a combination of moisture in the slab from ground water and blocked/backed up drainage system. The migrating corrosion inhibitor may have also contributed to elevated moisture levels, insufficient primer penetration and contamination of the concrete surface if not prepared, leading to coating delamination.
Other surface damage across all levels was apparent with considerable concrete repairs required throughout the car park amounting to 3500m2 in total with:
• 323 on Level 1
• 27 on Level 2
• 376 on Level 3
• 47 on Level 4
• 29 on Level 5
• 40 on Level 6.
Included with our submission is a spreadsheet which details the size and dimensions of each concrete repair across each Level. Special equipment was used to prepare the deck without damaging the concrete slab including hydraulic and pneumatic tools including:
• Bobcat Skidsteer with a Rotary Planer attachment which was used to remove the 6mm of the existing coating without further damaging the concrete below
• MP6000 Ride On Shot Blasting Machine which was used after the Bobcat Skidsteer to clean the concrete and provide a better key for application of the Triflex Waterproofing System.
The proposed project specification by Triflex Technical Team was the proven Triflex Deckfloor system. The multiple conditions on the various car park levels meant that there were extensive challenges regarding the extent of preparation to every concrete deck. The Triflex Deckfloor based system achieved very strong adhesion after all concrete treatments were carried out in preparation for the waterproofing coating.
The reinforced liquid applied membrane could easily accommodate the complex forms and details. With elastomeric properties, the system can cope with the various requirements for crack bridging as well as being durable with high impact and abrasion resistance.
Taking cognisance of the traffic that this carpark would endure, Triflex Quartz was utilised on the car parking spaces and Triflex Emery aggregate was utilised on ramps and main drive areas throughout the various levels.
SPECIFIC INSTALLATION METHODOLOGY
Due to the extensive shot blasting, concrete repairs and infills throughout the car park, a specific methodology had to be followed which captivated dust, ensured defective concrete repairs were deemed suitable for overlay prior to the application of products and ensured appropriate curing and drying time of each applied product. The methodology and sequence of works included:
1. The locations of the concrete repairs marked out, numbered and recorded as a repair
2. The perimeter of the repairs cut using a cut off circular saw, the depth of the cut was approx. 20mm, to prevent a feather edge
3. The defective concrete was removed using a handheld breaker and compressor with extra care taken to ensure all loose material is removed
4. Any exposed reinforcement within the broken-out section was wire brushed and primed
5. Any damaged reinforced rebar was replaced
6. Cement mixed in accordance with the manufacturer’s instructions
7. Cement poured level with the existing substrate
8. Grind the concrete when dry and leave ready for overlay
Triflex Installation Methodology (All drying and curing times were within an hour)
9. An air compressor was used to blow clean all the shot blasted concrete ensuring a clean and debris clear surface before Triflex application
10. All areas of concrete primed using Triflex Cryl Primer 287 cross rolled in two directions
11. Any metal, railings etc. Buffed using hand grinder with metal flap disks and primed using Triflex Metal Primer
12. Small exit area with Asphalt, primed using Triflex Primer 222 cross rolled in two directions
13. Any small areas of damage, holes or fine cracks were filled by trowel using Triflex Cryl Spatchel
14. Any upstands were complete to a minimum of 150mm using Triflex Pro-detail immediately followed by embedding the reinforcement fleece and immediately applying a further coat of pro-detail.
15. All Cracks and joints including those of the concrete repairs were then treated with crack banding. Which consists of applying one coat of Triflex Propark, a 250mm wide fleece was then laid while coating was still wet and embedded by a further coat of Triflex Propark. Material applied using a roller
16. To level out areas of poor concrete surfaces a scratch coat was then applied by towel using Deckfloor RS and filler sand
17. Once all repairs above were complete a basecoat of Triflex RS was then applied by way of stub roller. Triflex Quartz was immediately lain on to the Wet Deckfloor Rs ensuring there were no wet patches visible. Triflex Emery (more durable/ hardwearing) was used for all turning points and ramps
18. All areas were blown clean with air compressor of the loose Quartz/ Emery, where possible the loose material was recycled for reuse in the next areas.
19. The topcoat, Triflex Finish 209 was then applied using a hard squeegee and back rolled using a wide dry roller, rolled in one direction. All different colours for different parking bays and road were marked out and separated by masking tape to give straight lines.
20. Finally, Triflex Preco Line 300 was used to complete the lines of parking bays and road markings.
MEETING THE CHALLENGES OF A BUSY RETAIL CENTRE
Upon commencement of the project, issues by retail tenants were raised regarding odour as the carpark was undergoing a major replacement of the ventilation system at the same time as the car park coating was being installed, it led to challenges around air movement within the car park levels.
We mitigated the odour issue by installing heavy duty extraction equipment to minimise risk together with air quality assurance testing carried out daily with readings recorded and issued to the client.
Considerable noise reduction and vibration concerns were addressed by conducting noisy and disruptive works out-with normal working hours to ensure that retail stores could continue trading without disruption during normal working hours.
An additional challenge due to the car park being enclosed was to ensure adequate ventilation and dust suppression measures were in place to meet the highest of standards in regard to the Health and Safety requirements for operatives, members of the public and retail tenants. There were no health and safety accidents, incidents or RIDDORs.
Consideration was always given to deliveries and operatives vehicles visiting the site to ensure no impact on the day-to-day operation/servicing of The Thistles Shopping Centre. Traffic management was paramount and was expertly managed by our dedicated Site Management Team.
- Gallery
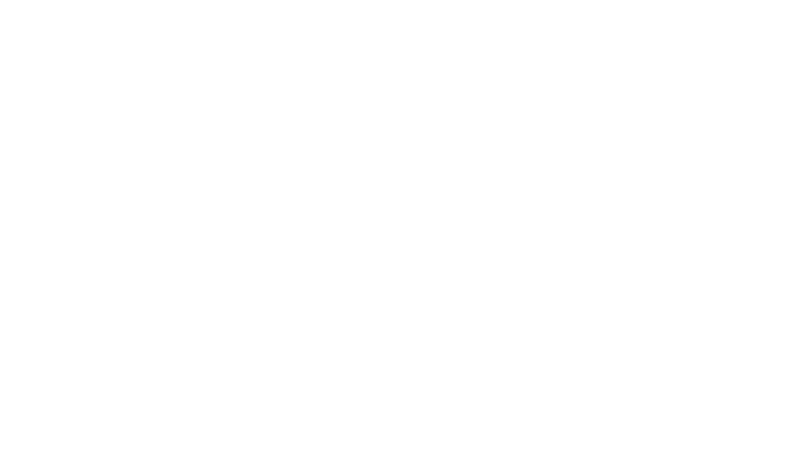
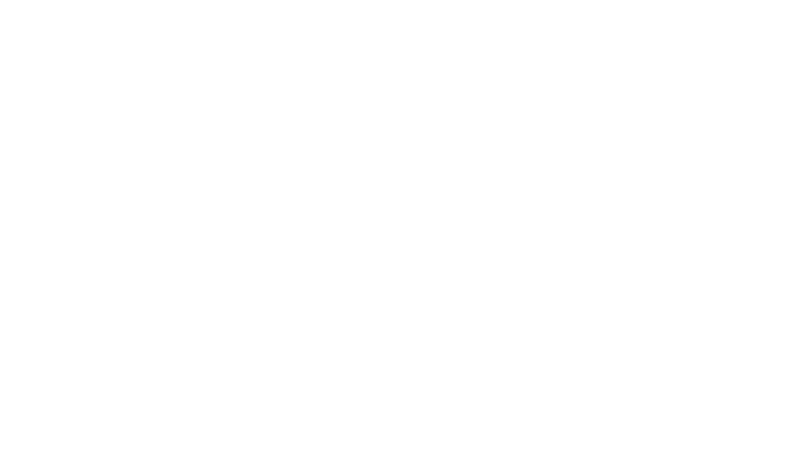
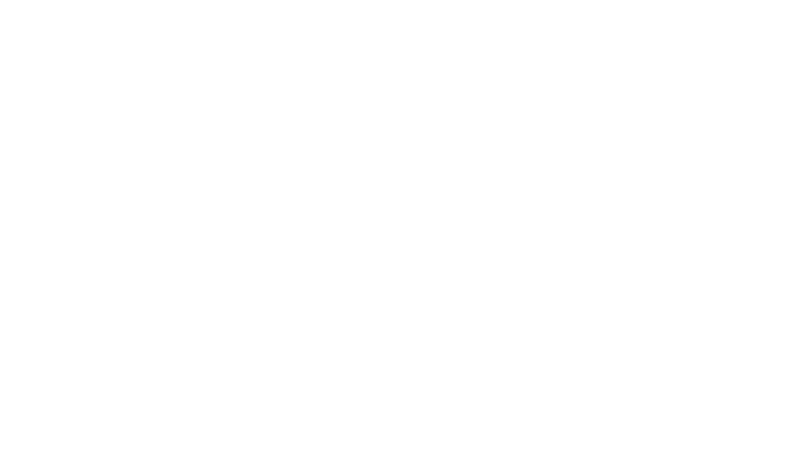
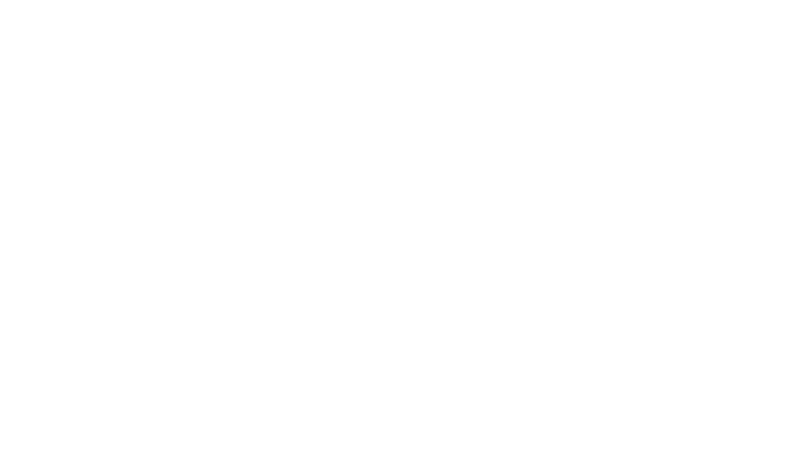
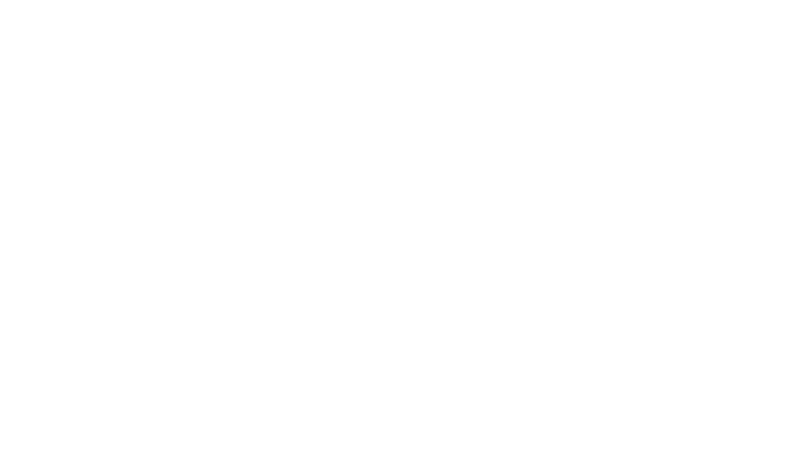
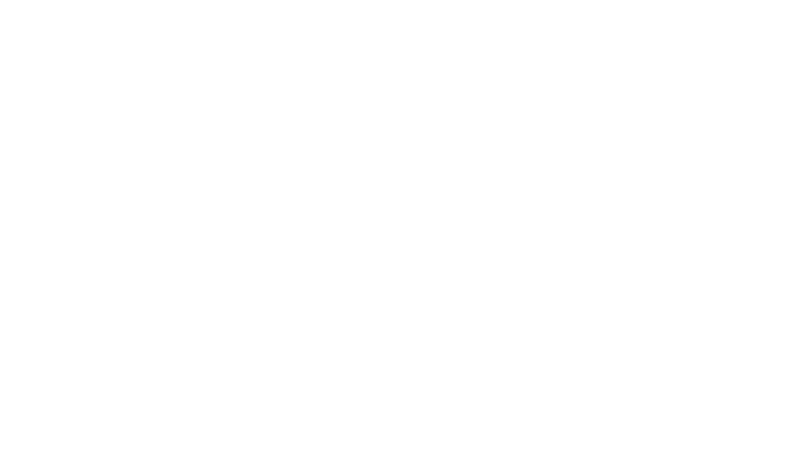