40 Leadenhall & 19-21 Billiter Street EC3 - Proteus Waterproofing Ltd
Project
40 Leadenhall & 19-21 Billiter Street EC3
Product
Proteus Hot Melt and Cold Melt
Size (M2)
5381.1m2
Contractor
ARC Waterproofing
Winner
LRWA Awards 2025 - Highly Commended - Sustainability Project of the Year
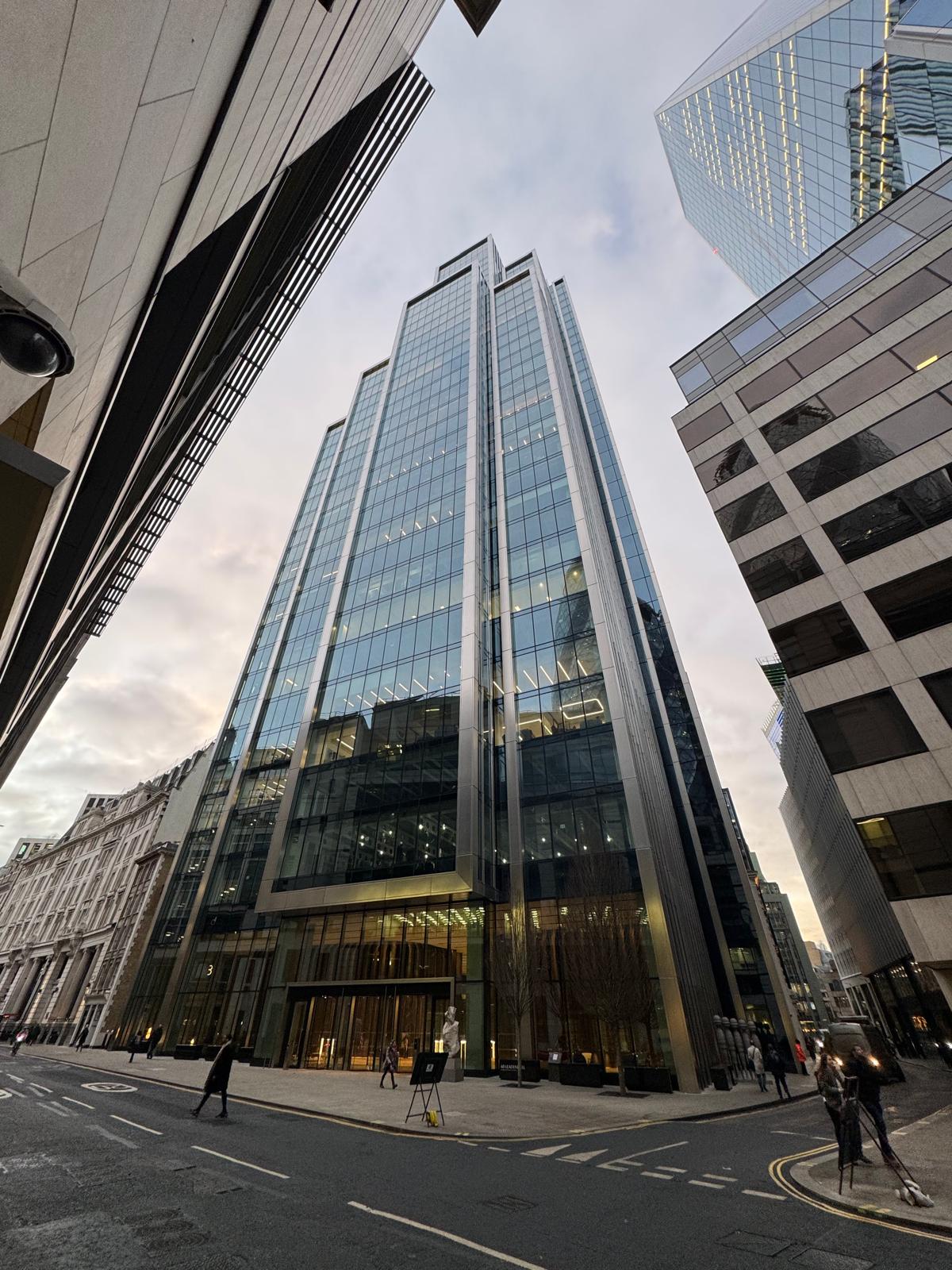
- The Background
Located in the City’s insurance district, 40 Leadenhall is one of the biggest schemes to ever receive planning permission in the City of London, as well as the largest office development completed in London in 2024.
Perfectly placed between Aldgate, Bank, Spitalfields and Southwark, 40 Leadenhall is a newly built 910,000 square-foot innovative lifestyle hub that sits at the centre of it all.
The development has acquired the moniker of ‘Gotham City’, in homage to the densely built hometown of Bruce Wayne. Built on big ideas, this business destination provides an exceptional environment that seamlessly blends business and life, where every detail is elegantly considered to enhance employee’s days, both personally and professionally.
Towering at an incredible 34 storeys high, 40 Leadenhall boasts 80,000 square-feet of amenity space, a 22,500 square-foot treatment and changing area, a wellness suite, library, a 30-seat HD cinema room and five independent retailers. Staff are able to use touchless technology to book spaces at the 200-seat auditorium and two public restaurants.
Employees can flow effortlessly from morning workouts, to afternoon meetings and rejuvenate in one of the 17 outdoor green spaces. With four communal terraces that offer every occupier refreshing outdoor space, residents can also escape the daily grind with free access to the exclusive ‘residents only’ rooftop clubhouse, a place truly designed with biophilia in mind.
The building responds beautifully to its surrounding context while making its own confident statement within London’s famous skyline. The design recalls the classic North American skyscrapers of the early 20th century consisting of several stepped blocks, which terraces cascading down from the city cluster towards the River Thames and the Tower of London, similar in appearance to the Gotham City Skyscraper. It steps back on Leadenhall Street to respect its historic surroundings and protect views of St Paul’s Cathedral.
The design also includes the restoration and integration of the Grade II-listed heritage building, 19–21 Billiter Street into the project, adding additional timeless and elegant amenity space, while protecting heritage assets.
Working in partnership with industry leading contractors and architects with strong and ambitious social values, Proteus Waterproofing®, and Proteus approved Contractors, ARC Waterproofing Ltd, were able to work collaboratively on the many terraces, roofs and roof garden areas to the North Tower, South Tower and Billiter Street, intertwining their ethical responsibility to consider sustainable environmental, social, and economic factors into building designs.
- The Challenge
40 Leadenhall was designed to create a neighbourhood, not just a business. With the health of the people and the planet at the forefront of importance, it was crucial to determine the needs of the client.
Conventional London office buildings typically provide no benefits to the environment and offer inadequate green space to building users. As Proteus Waterproofing® were present at the initial design stages of the building, this issue could be eliminated from the start.
Once the main contractor had been appointed, discussions commenced with the roofing contractor, ARC Waterproofing Ltd. Both ARC and the envelope manager of MACE approached Proteus Waterproofing® due to their outstanding reputation built up from successful partnerships with both parties on previous projects. Proteus immediately began working with their design team to finalise a proposal for the roof waterproofing and insulation with the inclusion of Green Roofs.
The design element presented numerous complexities due to the significant amount of terrace areas. Proteus’ inhouse Technical Design Team completed numerous weighted U-value calculations to determine the required insulation thicknesses to meet the thermal performance requirements of the building. As the threshold details and finished floor levels varied across the different areas, Proteus had to be selective in their choices of insulation. Fortunately, Proteus Waterproofing® provide an extensive range of insulations and were able to combine their Proteus Pro-Therm XPS Plus, and Foamglas insulation to achieve the required thermal performance.
Due to the significant scale of the building and the extent of work that was required, the logistics programme had to be meticulously organised, but equally flexible. The client would issue specific dates in which the waterproofing works could commence. This meant that the programme of installation was incredibly randomised to allow for various other trades to complete their works at the same time. This provided an abundance of challenges as the waterproofing contractors were heavily reliant on other trades completing their works effectively to allow them to begin theirs. When other trades were facing issues with deliveries and unplanned incidents, it had a knock-on effect to ARC and Proteus who had to continuously delay works and reschedule deliveries.
Arranging deliveries for this project put an immense amount of pressure on the Proteus Sales Admin Team, who were in constant contact with ARC Waterproofing throughout the entire order process. The central location of the project meant all site access gates used for deliveries were located on extremely busy roads. As there were several deliveries from various trades arriving daily, deliveries were time limited and had to be arranged through a booking system, managed by MACE, to determine which gate the orders could be delivered to.
Some gates were only suitable for forklifts, some could only facilitate small vans, and others could accommodate larger vehicles including articulated lorries and 7.5tonne tail lifts. As the works progressed, the number of access gates were reduced making it incredibly challenging for Proteus to arrange the correct vehicle types for the required times. This system, on top of the continuous delays and constant rearranging of deliveries proved to be a logistical nightmare for the Proteus Team and ARC Waterproofing.
Due to the scale of the building, there was an extreme demand for hoists and cranes to move materials to their correct locations. This was also managed by MACE and required a booking system which added another layer of complexities to the delivery and order process. ARC constantly had to compete with other trades to ensure they had the correct machinery to efficiently move their products once the deliveries had been completed.
The waterproofing works were completed in several phases over the various terrace areas due to the ever-changing programme of installation. This meant a lot of the works had to be completed in a varying sequence, continuously moving around different areas of the building.
The works on the North Tower were spread across 9 different levels, with a total of 12 terrace areas to complete. Proteus Hot Melt® was the leading waterproofing system of choice for this project as it is ideally suited to inverted new build projects. Installation is quick and simple, yet still provides a robust and watertight finish. It is certified by the BBA and will provide a durable waterproofing for the service life of the roof in which it is incorporated in.
On level 37, Pro-Prime® Bitumen was applied to the concrete substrate, waterproofed by the Proteus Hot Melt® system, extended over the pitch pockets, balustrade posts and roof penetrations. This allowed for the installation of the Proteus Low K Water Reducing Layer and concrete paving finish.
Level 36 required a mixture of insulations to ensure the thermal performance could be achieved. On the areas where plant was situated, the Proteus Hot Melt® system was installed, followed by Proteus Pro-Therm XPS Plus insulation, completed with concrete slabs. This application was also mirrored on Level 35. On the maintenance route that was visible from the building, Foamglass insulation was installed above the Proteus Hot Melt® system and finished with paving and ballast to provide a more aesthetically pleasing finish.
Office balconies were built on Levels 34-31, as well Level 27, 25, 23 and 7 to provide employees with stunning views of the London skyline. The concrete deck was primed with Pro-Prime® Bitumen, to allow for the application of the Proteus Hot Melt® waterproofing. This was installed around the pitch pockets, balustrade posts and roof penetrations. Proteus Pro-Therm XPS Plus insulation was laid in conjunction with Proteus Low K Water Reducing Layer. The client chose to finish these terraces with granite paving slabs to integrate the luxurious feel from the inside out.
The South Tower was made up of 16 levels. Waterproofing works were spread across 6 Levels, with a total of 11 terrace areas to complete.
Level 16 had a variety of waterproofing requirements. Proteus Hot Melt® was not a suitable waterproofing system for the entire roof area as the smaller areas provided inadequate space for a boiler. Proteus Waterproofing® were able to provide a cold applied, and equally robust alternative. To ensure the lift overrun, external parapets, and intricate details could be seamlessly encapsulated and waterproofed, Proteus specified their Cold Melt® system.
As Cold Melt® is a cold applied liquid, the risk of fire from hot works could be completely eliminated. Cold Melt® exhibits extremely low odour meaning contractors and other trades were not affected by the smell of fumes.
The 16th floor also contained a large area of plant. The Proteus Hot Melt® system was installed on this area, followed by Proteus Pro-Therm XPS Plus insulation. This area was finished with concrete paving to provide a suitable surface for the plant.
To ensure this space was used to its maximum potential, a Green Roof was also installed on this area. A calculation of the entire building was completed to determine the total required amount of green space. Proteus Hot Melt® was the perfect waterproofing solution to use as it is compatible with various landscaping finishes including Green and Blue Roofs. The concrete substrate was primed with Pro-Prime® Bitumen ready for the Proteus Hot Melt® Waterproofing. All pitch pockets, balustrade posts and roof penetrations were protected by the Proteus Proteus Hot Melt® waterproofing to enable the installation of the Proteus Pro-Therm XPS Plus Insulation. Proteus Low K Water Reducing Layer was then installed to allow for the installation of the Pro-Living® Green Roof. Pro-Living® DR20 Drainage board was laid in conjunction with the Pro-Living® Filter Fleece and Pro-living Extensive Substrate and finished with the Pro-Living® Sedum Blanket and granite paving.
The same waterproofing and Green Roof installation was mirrored on Level 15.
Across Levels 13, 11, 9, 8 and 7, there were 9 terraces to complete. These terraces were primed with Pro-Prime® Bitumen and waterproofed with the Proteus Hot Melt® system. These areas were finished with granite paving to ensure the high-end thread that ran throughout the building’s interior continued through to the outside spaces.
As the concrete substrates were curing slowly on several of the terrace areas, it was vital to find a solution that would prevent the works falling further behind schedule. Proteus Waterproofing® were able to offer a solution to this unforeseen issue.
To bring the program back on schedule, Cold Melt® DPM Primer was first installed over the green concrete after only 3 days. The concrete below the primer, now protected from the elements, was allowed to continue its chemical hydration process and cure in its own time. Once the Cold Melt® DPM primer had cured overnight, it provided a dry surface for the Proteus Hot Melt® waterproofing system to be laid.
This waterproofing process allows trapped moisture to escape naturally overtime and is proven to create a stronger concrete base, giving the substrate a seamless and robust waterproofing protection and a lifetime guarantee as specified by the BBA.
As the glass balustrades were not being installed until the terrace areas had been completed, temporary balustrades had to be installed. Works were carried out wearing harnesses to allow the works to be safely completed on the permitter upstands and details.
There was several perimeter details and upstands across all the terrace areas, including balustrade posts and steel work where the capping was fitted. Waterproofing complex details at such height presents several challenges. These challenges were intensified by the harsh weather conditions and strong winds. As safety to the roofing contractors was paramount, works had to be postponed on several occasions. Works to these areas could only commence again when the weather conditions were more stable.
The refurbishment works for 19-21 Billiter Street were also integrated into the project schedule. The Grade II listed building, once home to the London Shipping Exchange, sits adjacent to 40 Leadenhall. Designed by Make Architects, the renovation has revived the 4-storey 19th century building and transformed the space to include multiple amenity spaces, a fitness and wellness centre, a salon and a Pelaton room which all reflect the superb new facilities of the wider development.
To bring this building into the 21st century, a Green Roof was installed on the 4th Level. As there were no cranes to lift a boiler for the Proteus Hot Melt® system, Cold Melt® was the ideal waterproofing of choice. To ensure the structural deck was completely flat, Proteus Fastfill was firstly installed. The concrete substrate was primed with Pro-Prime® SA, followed by Pro-Vapour Control/Carrier Membrane SA, to allow for the installation of the Cold Melt® waterproofing and the Pro-Living® Green Roof. Pro-Living® DR20 Drainage board was laid, followed by the Pro-Living® Filter Fleece and Pro-Living® Wildflower Substrate, finished with the Pro-Living® Wildflower Blanket.
The Pro-Living® Wildflower Blanket is grown with 32 UK native wildflower species and 2 non-invasive grasses. The species within the blanket are shade and drought tolerant requiring low maintenance. This benefit is an addition to the wealth of benefits Green Roofs provide to both the building and the building occupants.
To ensure the project was completed to the highest standard, it was crucial that ARC Waterproofing Ltd, Proteus Waterproofing Ltd, and the client maintained regular contact. Site inspections were carried out by Proteus Waterproofing to inspect the progress and installation of the works, offering product and application advice where necessary. Photographs were taken throughout each stage to evidence the high-quality installations.
Collaboratively, Proteus Waterproofing and ARC Waterproofing Ltd successfully overcame the abundance of design, installation and logistical challenges and delivered this project to an impeccable standard.
It’s clear to see why this project won the ‘Building innovation Award’ for the most innovative commercial project, and The Architects Company ‘City of London Building of the Year Award 2024’. The building targets BREEAM ‘Excellent’, and ‘Platinum’ WELL ratings, as well as being independently verified as one of SmartScore’s smartest buildings in the world. It’s one of the first UK office towers to achieve NABERS certification – an energy efficient standard that measures how a building is designed to operate and how it performs in use.
The ethical responsibility to design for the health of the people and planet runs effortlessly throughout this entire building. Designed with social, environmental and economical factors, this project truly provides an interconnected solution for the building and its users. Whether it’s bustling social spaces or quiet corners to stop and think, 40 Leadenhall really does have everything available to create a space for concentration, collaboration and innovation.
- The Solution
As waterproofing system suppliers, it is Proteus’ obligation to provide sustainable waterproofing solutions that are beneficial to both the client and the environment. This project ticked every box for the client.
As well as providing an aesthetically pleasing finish, Green Roofs provide numerous environmental, economic, and social benefits. Green Roofs uphold the integrity of the building envelope and decrease energy consumption by acting as an insulator. One of the biggest problems facing a typical roof is poor insulation, leading to substantial heat loss in winter and sweltering conditions over the summer months. By implementing a green roof, the client was able to improve energy efficiency for the building while creating more comfortable conditions for the residents. This, in turn, decreases the generation of CO2, significantly reducing damage to the environment. Green Roofs also attract a wide variety of wildlife including bees, butterflies and insects which are scarcely seen in built up, overcrowded city spaces. As well as lacking in biodiversity, cities have notoriously poor air quality which can have alarming effects on human health. Green Roofs can capture these micro air particles, significantly improving the air quality for the residents while providing aesthetically pleasing outdoor spaces. Proteus is also unique in its ability to provide a greener waterproofing solution. Unlike any other waterproofing membrane, Cold Melt® incorporates recycled rubber crumb and other organically grown products such as castor oil, contributing to Proteus’ beliefs and responsibility in providing sustainable and environmentally friendly solutions. Cold Melt® is certified by the BBA to last the lifetime of the substrate in which is installed on, providing the client with total peace of mind. It is a cold applied liquid, meaning the risk of fire could be completely eliminated. Cold Melt® exhibits extremely low odour meaning contractors and other trades were not affected by the smell of strong fumes. Proteus Pro-Therm XPS Plus, with a verified Environmental Product Declaration (EPD), demonstrates strong environmental credentials through several key features. It uses Hydrofluoroolefins as a blowing agent, which has a lower environmental impact compared to traditional agents and zero Ozone Depletion Potential (ODP). The manufacturing plant maintains ISO 14001, ISO 9001, and ISO 50001 certifications, showing commitment to environmental and energy management. Production waste is recycled back into manufacturing, while packaging materials are recyclable. The product typically lasts for the building’s lifetime and can be reused when mechanically fixed. When reuse isn’t possible, its high calorific value allows for energy recovery through municipal waste incineration. Proteus are not only committed to supplying sustainable waterproofing solutions, but also believe in responsible supply chain practices. From the project outset, Proteus worked closely with their suppliers to improve the supply chain. By forecasting what products would be required, Proteus were able to anticipate what would be in high demand and plan accordingly. To reduce the carbon footprint of insulation deliveries, Proteus instructed manufacturing and delivery of the entire project quantity of insulation, which was delivered in full loads to the Proteus distribution centre in Essex which is situated just 28 miles from the site. To accommodate this large delivery, their distribution centre had to be rearranged to provide suitable storage. Stocking the insulation in bulk enabled Proteus to supply the site ‘just-in-time’, and on demand, meeting the project’s challenging logistical requirements, including a number of weekend deliveries. Proteus further mitigated the carbon footprint by ensuring that full load quantities were delivered to site on each delivery. This reduced the number of journeys into the city and meant the waterproofing contractors had the material they required readily available. Proteus Waterproofing® are FORS Gold accredited. Gold accreditation is only awarded to operators who actively promote the FORS standard to their supply chain. Vehicles within the fleet must use efficient fuels and effective transport routes to minimise impact on the environment and contribute to a lower carbon footprint. Proteus Waterproofing® ensured all deliveries to this project were made on Proteus vehicles to reduce negative impact on the environment, as well as meeting the requirements of the site. Driven by a shared commitment to sustainability and environmental well-being, Proteus Waterproofing®, ARC Waterproofing Ltd, and all participating contractors worked together to successfully create a destination that believes sustainable change will benefit us all. Exceeding environmental and social benchmarks, 40 Leadenhall and 19-21 Billiter Street offer impeccably designed, sustainable workspaces. These buildings blend character, innovation, and striking design to create a significant and positive contribution to the surrounding area. The project was thoughtfully designed to prioritise longevity, ensuring the buildings meet both current and future workplace standards for energy efficiency, health, and well-being. |
- Gallery
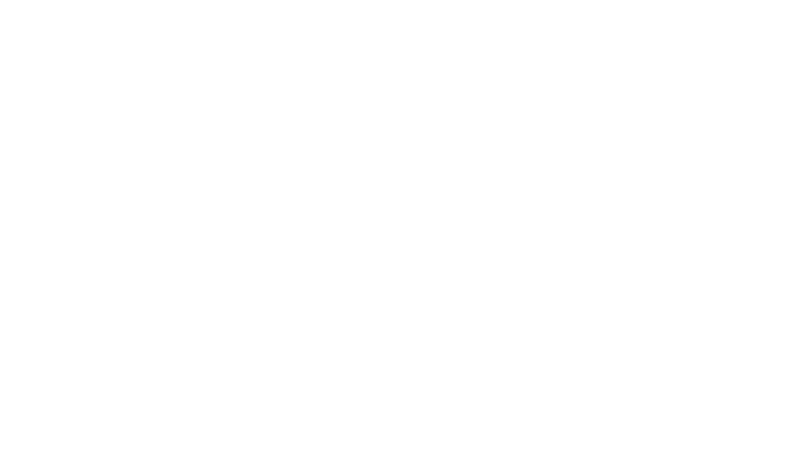
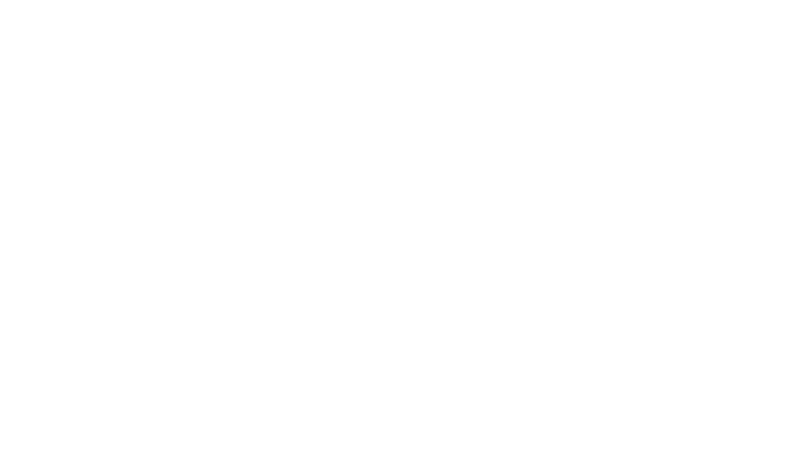
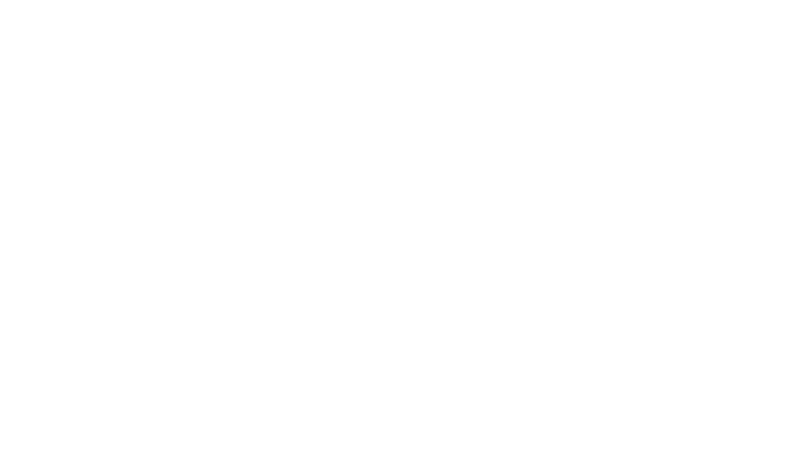
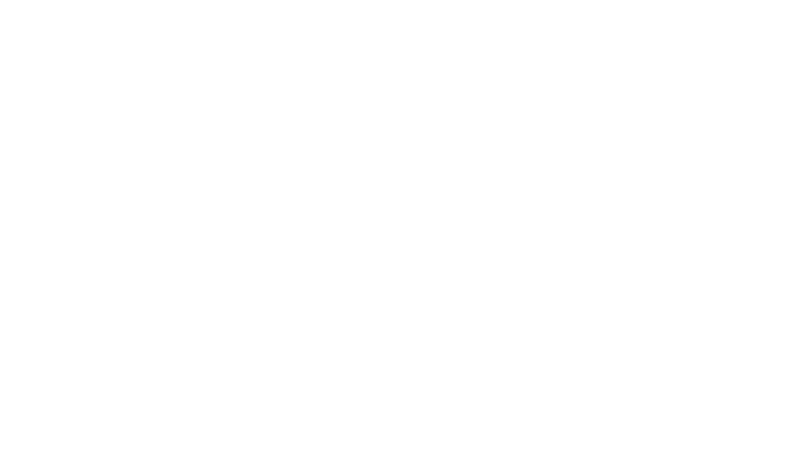
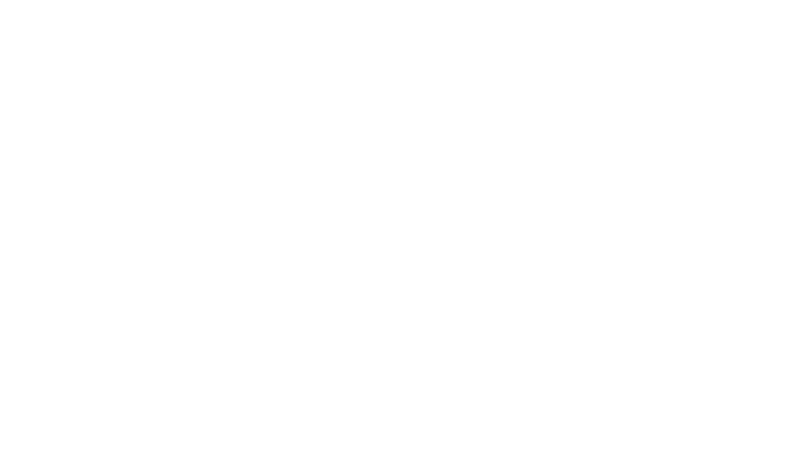
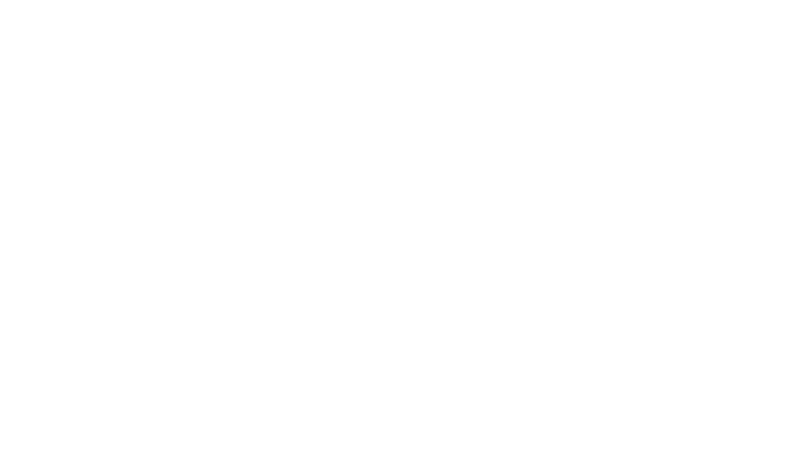