Marylebone House - Proteus Waterproofing Ltd
Project
Marylebone House
Product
Cold Melt and Pro-BV Plus
Size (M2)
850m2
Contractor
Essential Building Services
Winner
LRWA Awards 2025 - Highly Commended - Project of the Year in a Buried Application
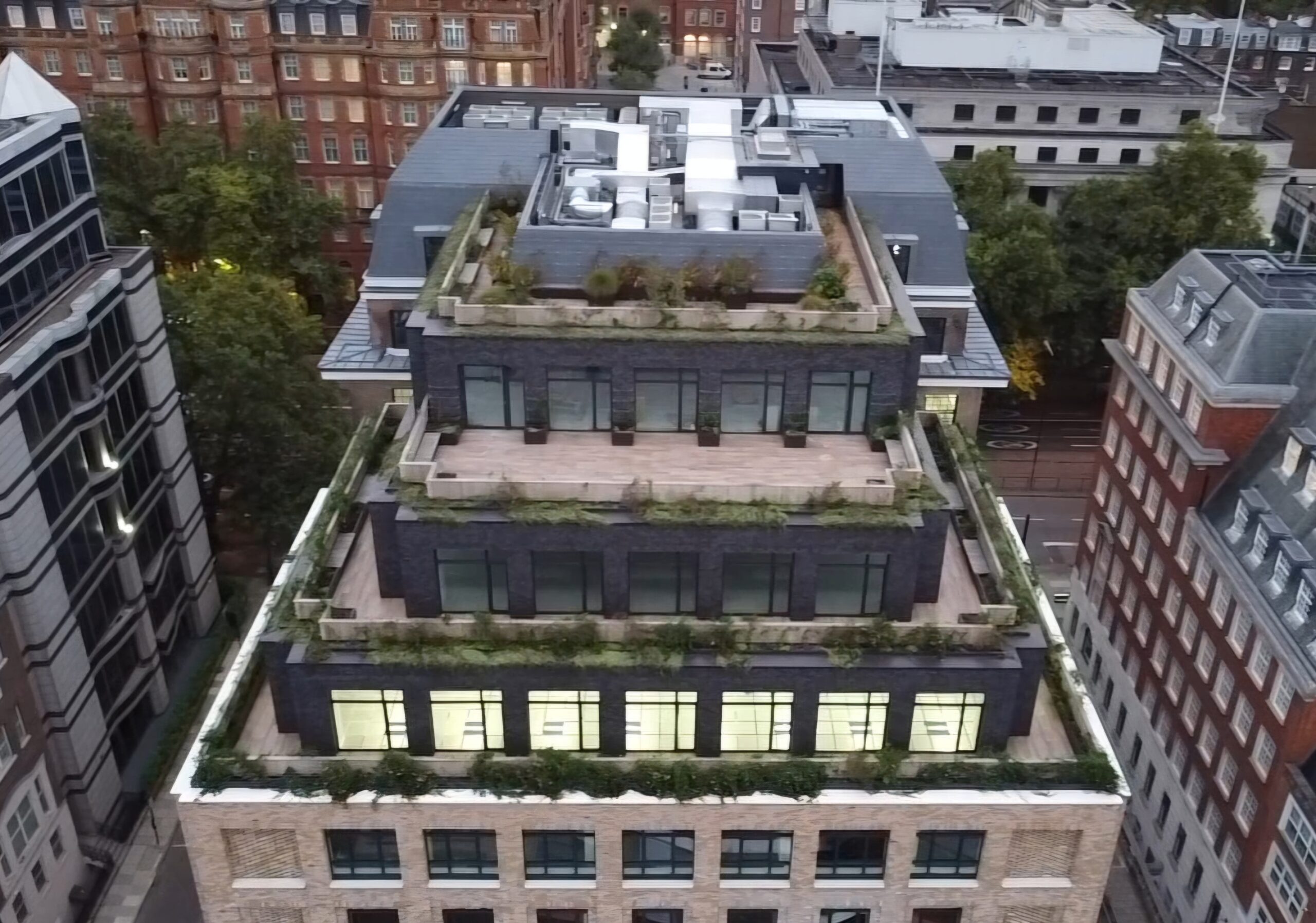
- The Background
With a highly visible location on Marylebone Road, and a short walk from Marylebone Station, Marylebone House has undergone a comprehensive and significant transformation.
Formerly owned by Arcadia Group, and the previous HQ for BHS, this neo-Georgian 1930s building has been converted into 75,000m2 of outstanding, sustainable workspace. Combining luxury interiors with intelligent design features, Marylebone House not only reduces its impact on the planet, but actively seeks to place sustainability, wellness and wellbeing at the forefront of importance.
Steeped in history yet designed to dance on the cutting edge, Marylebone House sustainably reimagines a tired office building to include an additional three storeys, set back on the upper levels, with tiered extensions to the south creating stepped and landscaped terraces from Level 6 upwards.
Extensive planting and landscaping were employed on the top four floors, including a communal Green Roof terrace at Level 9 to replace unsightly roof-based mechanical equipment with cascading plants and timber acoustic screens to restrict overlooking.
Furthermore, the contemporary three storey ‘Mews Building’ replaces a 1960’s incongruous and redundant car park building adjacent to Marylebone House. These newly built boutique offices, constructed from a lightweight Glulam and cross laminated timber structure, represent a saving of 19tCO2e compared to a more conventional concrete or steel alternative. In addition, the green roof on the mews building comprises 12 varieties of sedum planting, supporting acid grassland species and contributing to London’s biodiversity targets.
Appointed by Blenheim House Construction, Proteus Waterproofing®, and Proteus Approved contractors, Essential Building Services Ltd were tasked with completing these extensive refurbishment works to the roof and terrace areas, collaborating their visions of a greener more sustainable future for roofing.
- The Challenge
Marylebone House was tendered pre Covid-19, with the effects of the pandemic causing unavoidable delays and escalating cost increases. Proteus were approached by the main contractor as they had a number of successful previous projects, supported by their outstanding reputation to deliver cost effective, reliable, and sustainable waterproofing solutions.
Proteus immediately began working with Architects, Fletcher Priest, to put forward the improved technical proposals for the waterproofing and insulation design and calculations, with the inclusion of Blue and Green Roofs. Proteus Waterproofing’s inhouse Design Team were tasked with one of their most technical challenges to date. To align with the environmental goals of the project, Proteus had to meet the client’s complex waterproofing and thermal requirements, as well as provide a sustainable solution that would positively benefit both the building and the residents. Blue Roof calculations were completed to identify the required amount of overall Blue Roof space, and specific attenuation zone depth. The depth of the hard landscaping and pedestals to the terraces and the green roofs were also calculated, which then in turn identified challenging threshold heights available for the insulation. To find a solution, Proteus then generated an area weighted U-value calculation and utilised their vast array of insulations, in combination with their variety of waterproofing systems they have to offer, to ensure the building would meet the thermal and waterproofing requirements and conform with relevant codes of practice and fire performance regulations. Thermal calculations were completed on every area of the main building to ensure the optimum specified thermal performance of 0.17/m²K would be achieved. As the terrace areas had an aesthetic client requirement for no visible flashings along with level thresholds, and as the zone between the SSL and the FFL was incredibly tight, meeting the thermal targets without increasing costs was incredibly challenging. The schemes had to be changed on numerous occasions to facilitate both the technical and aesthetic requirements without compromising either, to the point that Proteus had to design the main contractors thermal break courses with different thicknesses for each individual terrace, and collaborate with the manufacturer of the fenestration door and window systems to design a bespoke end point within the base of the framework to terminate the waterproofing into and confirm to all relevant Codes of Practice including BS6229. A schedule of works was provided to suit the building programme, ensuring each section of the building could be efficiently completed while allowing other trades to effectively work alongside. This meant a lot of the works had to be completed in a varying sequence, continuously moving around different areas of the building. Due to the central London location, deliveries had to be booked in specific time slots by the site managers, with consideration to other trades. As the small road had limiting parking restrictions, products had to be unloaded quickly but efficiently. Proteus worked with Essential Building Services throughout the material ordering process to ensure timed deliveries were arranged and the products arrived on time, without effecting the schedule of works or other trades. Level 6 was the largest wrap around terrace of the building. To ensure the structural deck was completely flat for the blue roof design to work efficiently, Proteus Fastfill was firstly installed. The concrete deck was then primed with Pro-Prime® SA, followed by Pro-Vapour Control/Carrier Membrane SA. Proteus Pro-Therm Rubber Crumb matting, Proteus Pro-Therm VIP insulation and Proteus Pro-Therm HP PIR Plus were secured with Pro-Bond Foaming Adhesive, to allow for the application of the Pro-Vapour Control/Carrier Membrane SA and Cold Melt® waterproofing. This build-up provided a suitable deck for the Blue Roof Installation. Pro-Living® Blue Box Geotextile, DD4 Drainage board, 80mm Blue Boxx and DD4FP Drainage Board were laid on top of the Cold Melt® system and completed with a gravel ballast layer and porcelain tile finish. Planters were placed around the perimeter of these areas to provide residents with an essence of nature and an aesthetically pleasing outdoor space. The same application was mirrored on the terrace areas for Level 7 and 8. Level 9 presented the most challenges due to the variety of applications across the roof area. The terrace area was primed with Pro-Prime® SA, followed by Pro-vapour Control/Carrier Membrane SA. Proteus Pro-Therm Rubber Crumb Mat, Proteus Pro-Therm VIP and Proteus Pro-Therm HP PIR Plus were adhered with Pro-Bond Foaming Adhesive, ready for the application of the Pro-BW® Plus Waterproofing. This terrace area was also finished with porcelain tiles, with the addition of planters around the perimeter to add to the aesthetics. The main area of Level 9 was used for the mechanical and engineering plant. To ensure a smooth substrate, the concrete deck was filled using Proteus Fastfill and primed with Pro-Prime® SA. Pro-Vapour Control/Carrier Membrane SA was laid in preparation for the Cold Melt® waterproofing. Proteus Pro-Therm XPS Plus was installed followed by Proteus Low K Separation Layer to allow for the installation of the Pro-Living® Blue Roof system. Pro-Living® Blue Boxx Geotextile was laid with the Pro-Living® DD5F Drainage Layer. Pro-Living® Blue Boxx HD 100mm and Pro-Living® DD5FP were then installed to enable the placement of the concrete slab finishes. The areas on Level 9 which did not require a Blue Roof were fully insulated and waterproofed with Pro-BW® Plus. The substrate was primed with Pro-Prime® SA followed by Pro-Vapour Control/Carrier Membrane SA. Pro-Bond Foaming Adhesive was used to bond the Proteus Pro-Therm Rubber Crumb matting, Proteus Pro-Therm VIP Insulation, and the Proteus Pro-Therm HP PIR Plus insulation. This was then Primed with Pro-Prime® SA, followed by the application of Pro-Vapour Control/Carrier Membrane SA and the Pro-BW® Plus waterproofing system. These areas were finished with porcelain tiles. Insulating buildings effectively offers a wealth of benefits to not only the building owner, but the environment as well. Thermally efficient buildings are a fantastic step in combatting climate change. They rely less on fossil fuels to heat the building, reducing greenhouse gas emissions. In turn, the reduction of energy consumption significantly reduces the cost of energy bills making it even more of an incentive to consider environmentally beneficial insulation solutions. The Mews building was a newly built addition to the project, transforming an obsolete carpark into stunning office space. The initial survey of the building determined that the existing car parking structure could not be adapted or retained. This had no effect on the architect’s commitment to a sustainable solution. A series of discussions with local stakeholders ensured that the outcome of the building remained sympathetic to its surroundings. The structure is constructed from lightweight glulam and cross-laminated timber, with exposed timber joinery that adds warmth and character to the interiors. This timber structure saved an additional 19 tCO2e of embodied carbon compared to a concrete alternative (using 50% GGBS). By reusing the majority of the existing frame and substructure, the development saved significant amounts of embodied carbon, reduced on-site time, and minimised disruption to the neighbourhood. The building is also fully electric, with openable windows that provide mixed-mode ventilation, ensuring a healthy and comfortable environment for its occupants. It meets current and anticipated energy, health, and wellbeing standards, and is designed for resilience and durability, ensuring a long and sustainable future. The resulting building is not only harmonious to the surrounding streets. With the addition of both a Blue and Green Roof, it offers an array of environmental benefits. Due to the unusual shape of the roof, installation was broken down into four sections. The pitched area of the roof was a Green Roof Installation. The concrete deck was primed with Pro-Prime® SA, followed by the vapour control layer. Pro-Bond Foaming Adhesive was used to adhere the Proteus Pro-Therm HP PIR Plus, which was then primed with Pro-Prime® SA. Pro-Vapour Control/Carrier Membrane SA was then applied to allow for the application of the Pro-BW® Plus waterproofing and the Pro-Living® Green Roof system. The Pro-Living® Easy Modular Tray was installed to the pitched area, providing a secure installation to the exposed slope, along with a Pro-Living® Drainage Trim and waterproofing strap to secure the modular green roof boxes to this area. The adjoining area had both a Green and Blue Roof installation. Pro-Prime® SA was used to prime the concrete deck. Pro-Vapour Control/Carrier Membrane SA was then applied, along with Proteus Pro-Therm HP PIR Plus insulation, adhered with Pro-Bond Foaming Adhesive. This area was suitably primed ready to receive the Cold Melt® waterproofing and Blue and Green roof installation. Pro-Living® Blue Boxx Geotextile was laid, followed by the Pro-Living® Blue Boxx and DR25 FP. This allowed for the installation of the Pro-Living® Filtration Layer, Biodiverse Growing Medium and Biodiverse Sedum Blanket. The area connecting this level to the upper level was fully insulated with Proteus Pro-Therm HP PIR Plus insulation and waterproofed with Pro-BW® Plus. The upper Level of the roof was also a Green Roof installation. The concrete deck was primed with Pro-Prime® SA, followed by Pro-Vapour Control/Carrier Membrane SA. Pro-Bond Foaming was used to adhere the Proteus Pro-Therm Rubber Crumb Matting, VIP insulation, and HP PIR Plus insulation, ready for the Cold Melt® waterproofing and Blue and Green Roof installation. Pro-Living® Blue Boxx Geotextile was laid followed by the Pro-Living® Blue Boxx and Pro-Living® DR25FP. This allowed for the installation of the Pro-Living® Filtration Layer, Biodiverse Growing Medium and the Biodiverse Finish. Most of the installation was completed during the harsh winter months making it easy for the construction programme to fall behind. Furthermore, the newly poured concrete being laid in the winter months would struggle to cure enough in 28 days to be overlaid, adding delays to the construction programme causing large financial costs to the contactor. Proteus Waterproofing were able to offer the solution to get the construction program back on target. To bring the program back on schedule, Cold Melt® DPM Primer was first installed over the green concrete after only 3 days. The concrete below the primer, now protected from the elements, was allowed to continue its chemical hydration process and cure in its own time. Once the Cold Melt® DPM primer had cured overnight, it provided a dry surface for the Cold Melt® waterproofing system to be laid. This waterproofing process allows trapped moisture to escape naturally overtime and is proven to create a stronger concrete base, giving the substrate a seamless and robust waterproofing protection and a lifetime guarantee as specified by the BBA. Incorporating Cold Melt® DPM primer into the waterproofing works helped significantly reduce the project completion time meaning works could get back on schedule and budget, delivering far beyond the client’s expectations. Collaboratively, Proteus Waterproofing and Essential Building Services Ltd successfully overcame the abundance of complex challenges and delivered this project to an impeccable standard, resulting in one incredibly satisfied client, and another fully protected, long lasting, watertight project. Both Marylebone House and The Mews Building are key examples of how office buildings can be built sustainably. The resulting workplace is fit for the 21st century, whilst retaining the essential character of this historic building. With its innovative, forward-thinking designs including extensively landscaped terraces and rooftop views over London, Marylebone Place now stands as an exemplar of retrofit and innovation in the heart of the city. The performance of the both buildings were subject to strict environmental criteria, targeting a BREEAM rating of ‘Excellent’, along with measures which included natural ventilation, low energy systems, reuse of the existing structure and reuse of recycled and recyclable materials, and comparable water consumption reduction of 40%, and CO2 of 51.8%, achieving environmental performance data of: Airtightness at 50Pa 1.5 m3/h.m2 (main building); 6.15 m3/h.m2 (mews building) As waterproofing system suppliers, it is Proteus’ obligation to provide sustainable waterproofing solutions that are beneficial to both the client and the environment. This project ticked every box for the client. As well as providing an aesthetically pleasing finish, Green Roofs provide numerous environmental, economic, and social benefits. Green Roofs uphold the integrity of the building envelope and decrease energy consumption by acting as an insulator. One of the biggest problems facing a typical roof is poor insulation, leading to substantial heat loss in winter and sweltering conditions over the summer months. By implementing a green roof, the client was able to improve energy efficiency for the building while creating more comfortable conditions for the residents. This, in turn, decreases the generation of CO2, significantly reducing damage to the environment. Green Roofs also attract a wide variety of wildlife including bees, butterflies and insects which are scarcely seen in built up, overcrowded city spaces. As well as lacking in biodiversity, cities have notoriously poor air quality which can have alarming effects on human health. Green Roofs can capture these micro air particles, significantly improving the air quality for the residents while providing aesthetically pleasing outdoor spaces. Incorporating Blue Roofs into the design fundamentally contributes to the prevention of flooding. This is especially prevalent in densely populated urban areas where impervious surfaces dominate the landscape. The controlled release of rainwater from blue roofs also promotes water conservation by reusing rainwater for irrigation or other non-potable purposes, creating a more sustainable building. Proteus is also unique in its ability to provide a greener waterproofing solution. Unlike any other waterproofing membrane, Cold Melt® incorporates recycled rubber crumb and other organically grown products such as castor oil, contributing to Proteus’ beliefs and responsibility in providing sustainable and environmentally friendly solutions. Cold Melt® is certified by the BBA to last the lifetime of the substrate in which is installed on, providing the client with total peace of mind. It is a cold applied liquid, meaning the risk of fire could be completely eliminated. Cold Melt® exhibits extremely low odour meaning contractors and other trades were not affected by the smell of strong fumes. Pro-BW® Plus is one of the few waterproofing systems with a verified Environmental Product Declaration (EPD), demonstrating strong environmental credentials. It features a long service life of at least 25 years when exposed, significantly reducing replacement frequency. As a cold-applied system, it requires minimal energy during installation. The system can be easily overlaid rather than removed during renovations, minimising construction waste. Its durability and installation flexibility make it particularly sustainable for both new construction and refurbishment projects. Proteus Pro-Therm XPS Plus, with a verified Environmental Product Declaration (EPD), demonstrates strong environmental credentials through several key features. It uses Hydrofluoroolefins as a blowing agent, which has a lower environmental impact compared to traditional agents and zero Ozone Depletion Potential (ODP). The manufacturing plant maintains ISO 14001, ISO 9001, and ISO 50001 certifications, showing commitment to environmental and energy management. Production waste is recycled back into manufacturing, while packaging materials are recyclable. The product typically lasts for the building’s lifetime and can be reused when mechanically fixed. When reuse isn’t possible, its high calorific value allows for energy recovery through municipal waste incineration. Proteus Pro-Therm HP PIR Plus demonstrates strong environmental credentials through its excellent thermal performance, helping reduce building energy consumption and associated carbon emissions. The polyurethane insulation boards provide long-lasting thermal efficiency, with service life typically matching the building’s lifetime. The product helps minimise heating energy consumption in both new and renovated buildings. Manufacturing facilities maintain high environmental standards, and production waste can be recycled back into the manufacturing process. The boards’ durability reduces the need for replacement, while their thermal conductivity contributes to overall building energy efficiency and sustainability goals. Proteus Pro-Therm VIP demonstrates exceptional environmental performance through its outstanding thermal conductivity (as low as 0.008 W/mK), allowing for significantly thinner insulation layers while achieving the same thermal performance as conventional materials. This reduced material usage contributes to resource efficiency and lower transportation impacts. The vacuum insulation panels help minimise building energy consumption throughout their service life, which typically matches the building’s lifetime. Their slim profile is particularly valuable in renovation projects, helping to preserve existing structures rather than requiring new construction. When properly installed and protected, VIPs provide long-lasting thermal efficiency, reducing the building’s operational carbon footprint. Proteus Pro-Therm Rubber Crumb Mat demonstrates strong environmental credentials through its use of recycled rubber materials, supporting circular economy principles. The product is manufactured in facilities certified to ISO 9001, ISO 45001, ISO 14001, and ISO 50001, showing commitment to quality and environmental management. Its excellent acoustic and impact performance helps create more sustainable buildings, while its durability ensures long-term performance without degradation. The material is both mildew and moisture resistant. Being 100% recyclable at end of life and manufactured using recycled content further enhances its environmental benefits. Proteus are not only committed to supplying sustainable waterproofing solutions, but also believe in responsible supply chain practices. From the project outset, Proteus worked closely with their suppliers to improve the supply chain. By forecasting what products would be required, Proteus were able to anticipate what would be in high demand and plan accordingly. Proteus Pro-Therm HP PIR Plus is procured in Europe and played a crucial part in the thermal build up on several of the roof areas. Due to its lightweight qualities, Proteus were able to arrange this delivery to combine with a membrane delivery for another project, meaning only one journey from Europe to the UK had to be completed. Combining this delivery significantly decreased the transportation distance, reducing carbon emissions by 50%. Proteus Waterproofing® are FORS Gold accredited. Gold accreditation is only awarded to operators who actively promote the FORS standard to their supply chain. Vehicles within the fleet must use efficient fuels and effective transport routes to minimise impact on the environment and contribute to a lower carbon footprint. Proteus Waterproofing® ensured all deliveries to this project were made on Proteus vehicles to reduce negative impact on the environment, as well as meeting the requirements of the site. United by a shared belief in sustainability and the good of the environment, Proteus Waterproofing®, Essential Building Services Ltd, and all contractors involved were able to collaboratively transform this project. Serving to surpass environmental and social standards, both Marylebone House and The Mews Building bring impeccably and sustainably designed workspace to life. The result is a characterful, contextual, yet striking set of workspace buildings that make a positive contribution to the area. This project has truly been designed with the focus on delivering buildings that have long life spans and are able to meet current and anticipated workplace energy performance, and health and wellbeing standards. |
- Gallery
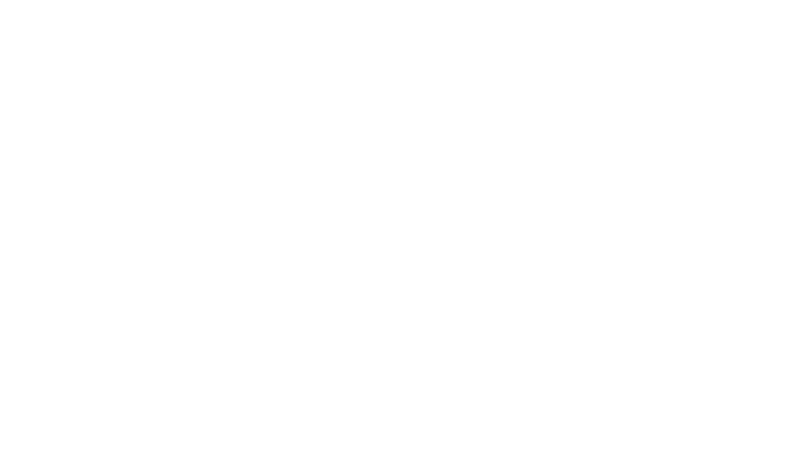
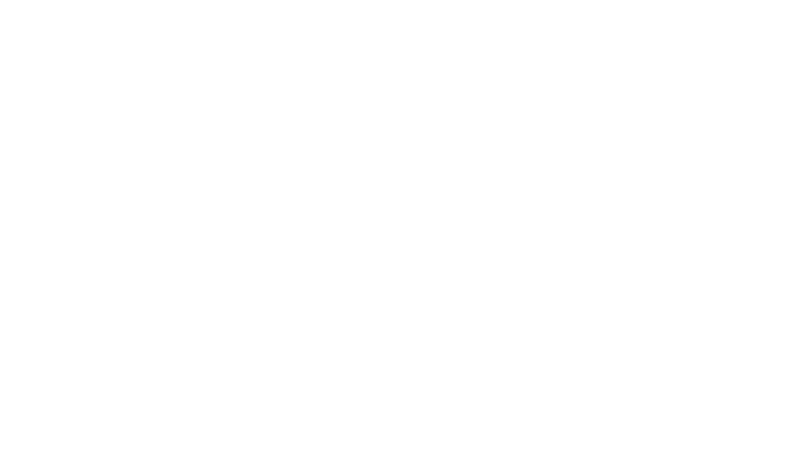
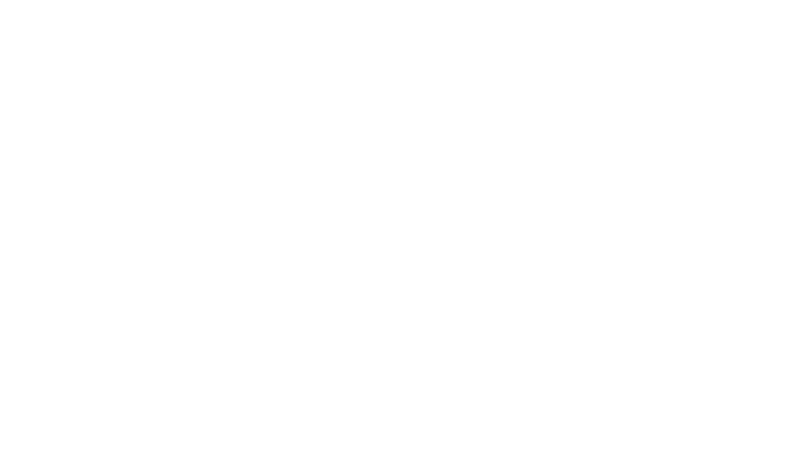
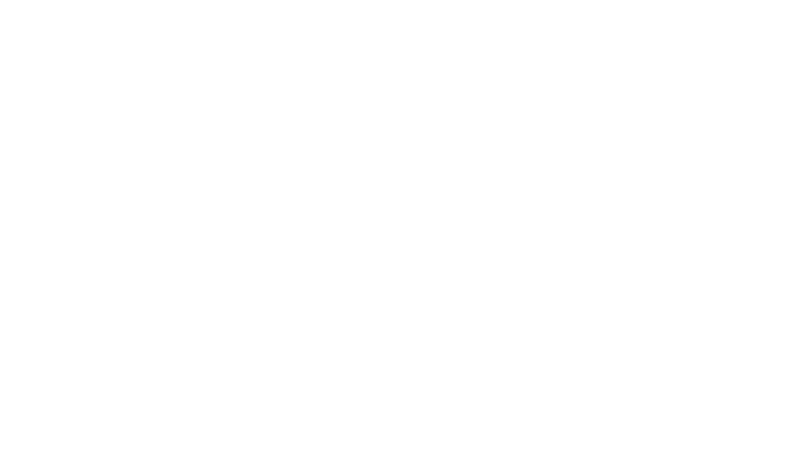
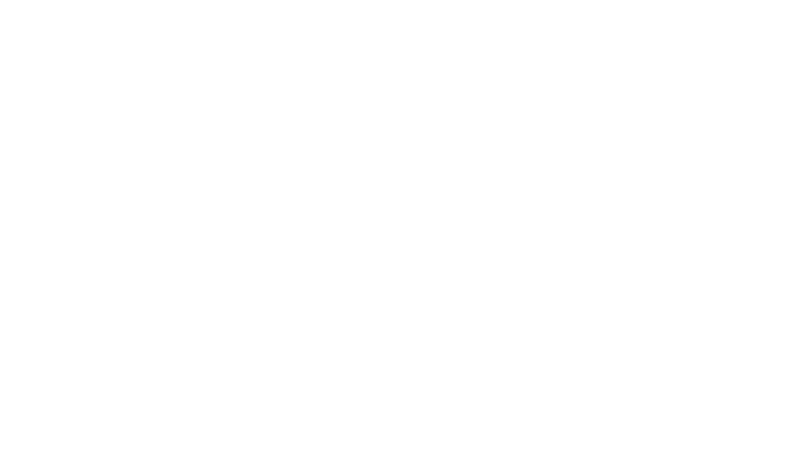
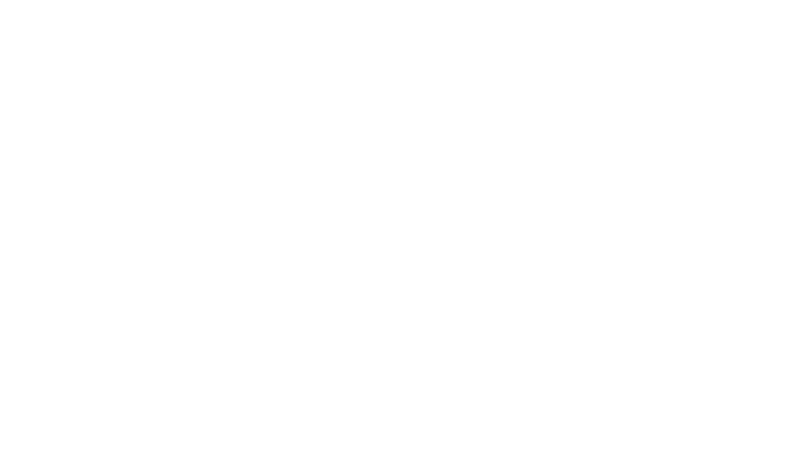