IKEA, Reading - Makers Construction Ltd
Project
IKEA, Reading
Product
Triflex DeckFloor
Size (M2)
9600m2
Contractor
Makers Construction Ltd
Winner
LRWA Awards 2023
Liquid Waterproofing Project of the Year
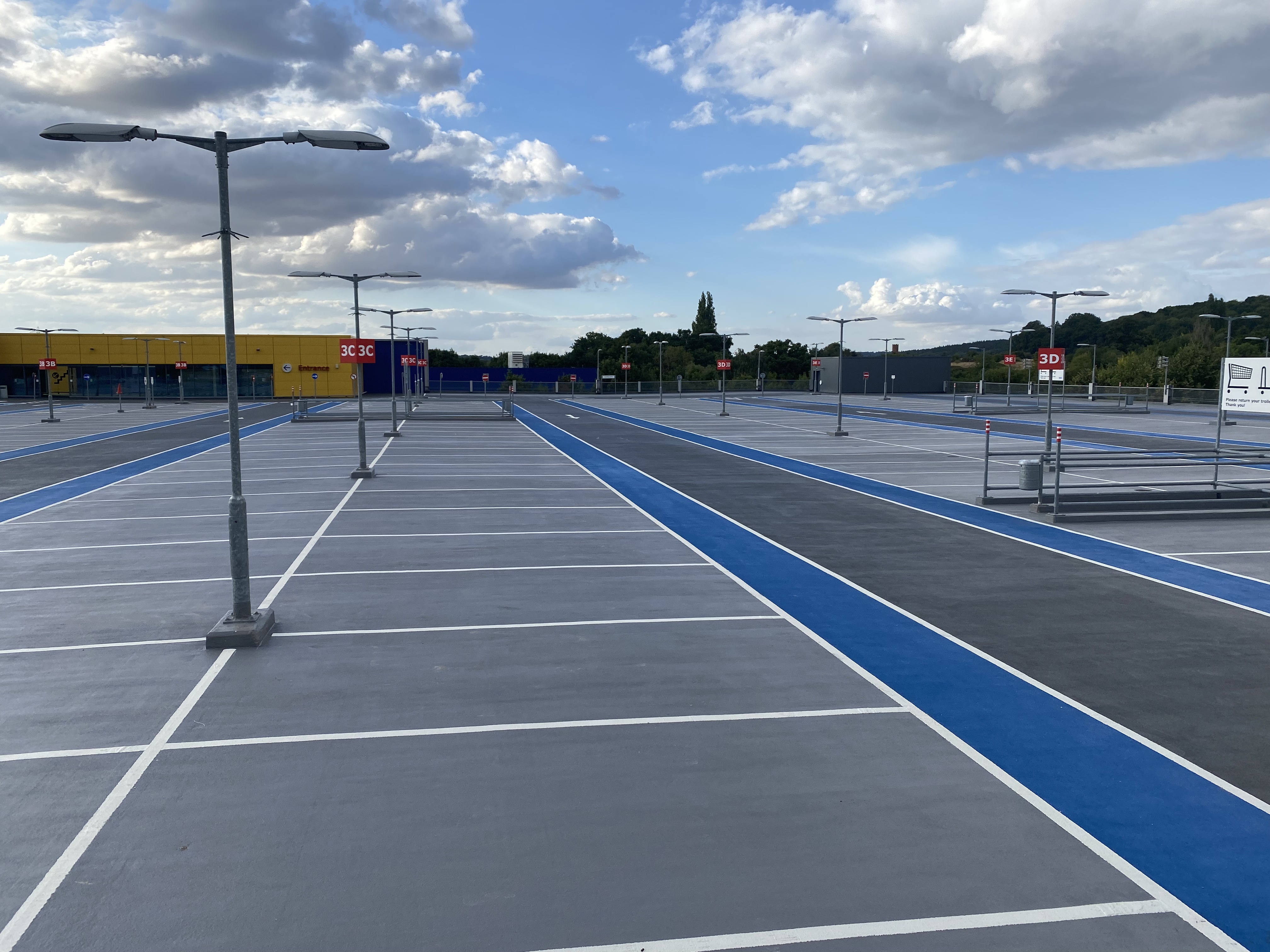
- The Background
The Ikea Superstore and multi-storey car park in Reading was constructed in 2016. The car park consisted of 4 floors using a steel frame, precast plank and structural topping configuration providing 1000 parking spaces for visiting customers. Two years after its initial build, the car parks original coatings were already demonstrating signs of failure. Failure so soon after the installation of a liquid coating is not normal.
- The Challenge
This car parking project surrounds huge interest due to the investigation into the failure of the original coatings and solutions to the problems realized. Through research and testing this car parking project had to decipher the chemistry behind liquid waterproofing systems and their build up and how this interacts with the substrates to which they are installed. In this project, new chemical solutions were developed to mitigate against issues in the car park decking slab. This testing, investigation and development further demonstrates the ability of Liquid Waterproofing as a long-lasting, highly effective waterproofing solution and its adaptability in its application. Problem Issues with the original car park installation were noticed following a routine maintenance inspection, some two years after the initial build, in 2018. The car park surface was showing some initial small blisters in isolated areas. The ring-shaped pattern was not immediately obvious but signs of “outgassing” seemed to proliferate to other areas, with some parts of the system becoming de-bonded mainly in the main drive isles due to cyclical traffic movements. This should not be occurring so soon after installation. During investigations into the issues, samples of the membrane were removed from site together with a series of cores through the structure. These samples sent away to laboratories in Germany, Switzerland, and the UK for a series of tests to be conducted upon them. Despite initial thoughts of “trapped moisture” issues, no liquid was present when the blisters were investigated on site.
Samples of the removed system were subjected to Gas Chromatography Mass Spectrometry (GCMS) to identify the chemical DNA of the system. This work identified that the original system had not achieved a full cure. That the process had been inhibited resulting in volatiles or gas being present within the system. Moreover, Differential Scanning Analysis (DSC) Thermal Analysis, was also undertook. The DSC testing underlined that the polymerisation process had been compromised with significant weight differences following the testing. After consultation of the installation documentation eliminated the theory of incorrect workmanship during the original car park works, it was indicated that the issue could lie beyond the system itself. Therefore, concluding from the process of investigative elimination, the structural topping was identified as the potential remaining factor causing the failure in the coatings. Further testing of the slab and in particular adhesion tests were carried out two years after the initial installation. Sixty-nine more adhesion tests were taken. A huge, 80% of the tests were inadequate, displaying cohesive failure within the upper layer of the structural topping and adhesive failure of the primer to the substrate. This interlayer adhesion failure, which should not be possible, lead experts to conclude that the slab had materially affected the curing/polymerisation process of the system. Whilst these detailed investigative works methodically unearthed the problems with the car parks original slab, the condition of the car park itself worsened. As the car park had remained operational during the two-year investigation, the progressive blistering, which now had manifested itself across the whole area, was beginning to de-bond and fracture. The test data had indicated that the systems initial bond was weakening and so it was decided that a repair option was not possible and a total replacement system was necessary for the Ikea Reading Car Park and mitigate against any further issues.
- The Solution
The investigations continued, and further concluded that the original construction programme in 2016 was behind schedule, and so, to reduce construction time, it is believed that plasticisers and curing membranes/agents were introduced into the structural topping design mix. It was discovered that this structural topping build-up had created significant issues in the curing and polymerisation to the original system. Therefore, a preparation and priming system needed to be designed that would negate perceived issues within the structural topping make up. Triflex UK undertook a series of core samples and modelling profiles which were then analysed in Germany. This further research and design investigation suggested that the best preparation involved the removal of the top 5mm of the structural topping and then to then treat the topping matrix with a “blocking chemistry” to prevent any free radicals from reacting with the proposed system. Triflex, therefore, specifically designed a specialist epoxy filled primer capable of flooding and filling the voids within the concrete matrix. This clever primer also provided enough stability and substance to neutralise any free radicals that could continue to react with the proposed acrylic PMMA system. During In June 2022, some six years after the original installation, 9600m2 of the system and 5mm of the structural topping were planned off and removed. It was decided that the works would take place in a single phase to eliminate the possibility of contamination. Adhesion tests were undertaken following the removal of the structural topping and were favourable. The car park was designed with 1000m of thermal expansion capability above the beam lines and despite the outgassing issues displayed on site the system had been free from reflective cracking. The existing sealants were removed and replaced with Triflex Flex Filler and then double banded to improve the tensile strength in these locations. To further complicate the project, during the installation process the external deck was subjected to rainfall and whilst waiting for the deck to dry out, dark lines were observed at 1.2m spacings following the orientation of the existing plank to plank layout. Once dried out these lines disappeared and became invisible to the naked eye but on closer examination micro cracking was discovered with cracks running in line with the plank-to-plank joints. The clever solution to this problem, looked to treat these using Triflex’s fleece technology, however, due to the substrate issues and chemistry design the deck had to be fully primed prior to the banding of these cracks. This meant that 7000m2of reinforcement had to be carefully mapped and treated after the primer application. These works had to be carefully planned and prioritised to not affect overall programme schedule. Once banded the Triflex Deckfloor System was applied creating parking bays and drive isles with dedicated pedestrian walkways. Numerous bollards, signs and impact barriers were removed and re-sited replacing the original mechanical fixings with resin fixings, which had proved so problematic following impacts by the general public causing the system to breach and allowing water into the structure. Thermoplastic line marking was installed to create individual bays, special parking provision and refuge areas. Specifications were upgraded to perceived high wear areas and Easel SJS movement joints were designed and incorporated between the ramps and car park structure. The main deck works were completed in 18 weeks following the extensive testing and investigation regime and the project is covered with a 10-year Warranty.This project truly demonstrates how clever research, design and workmanship over numerous years can come together to offer clients quality liquid waterproofing solutions to even the most advanced and complex of problems.
- Gallery
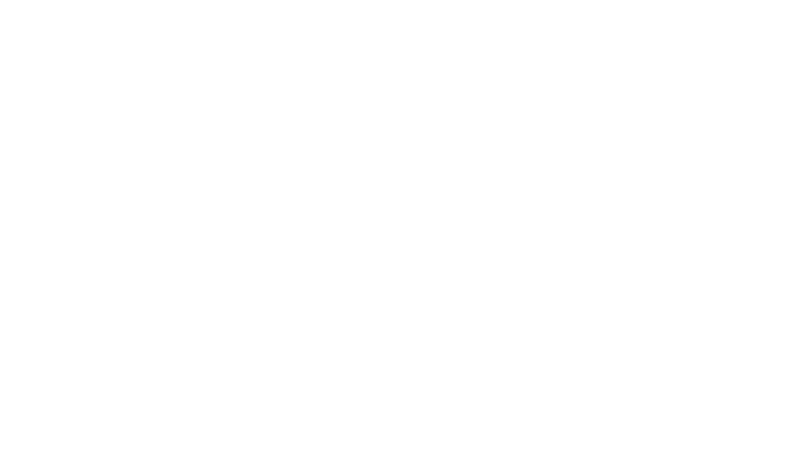
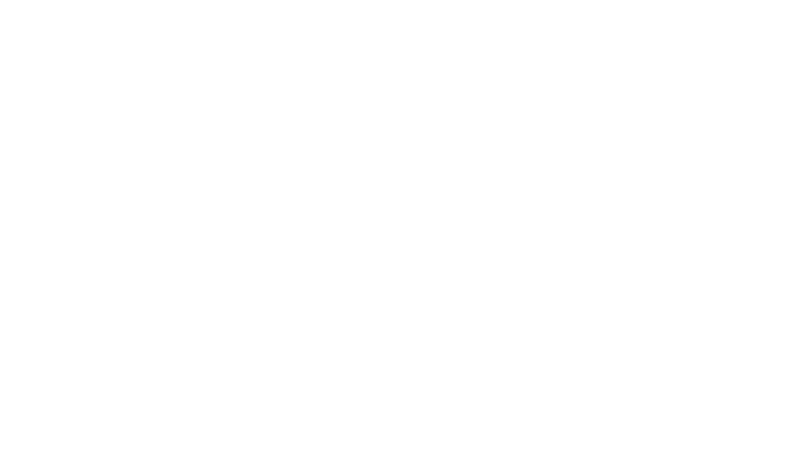
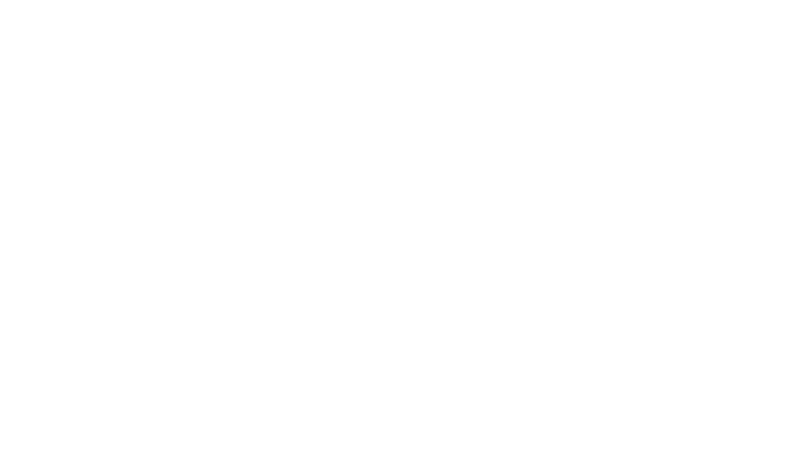
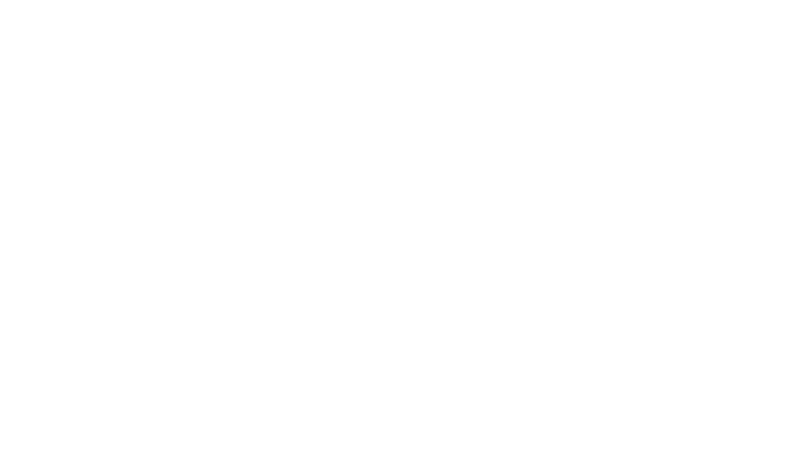
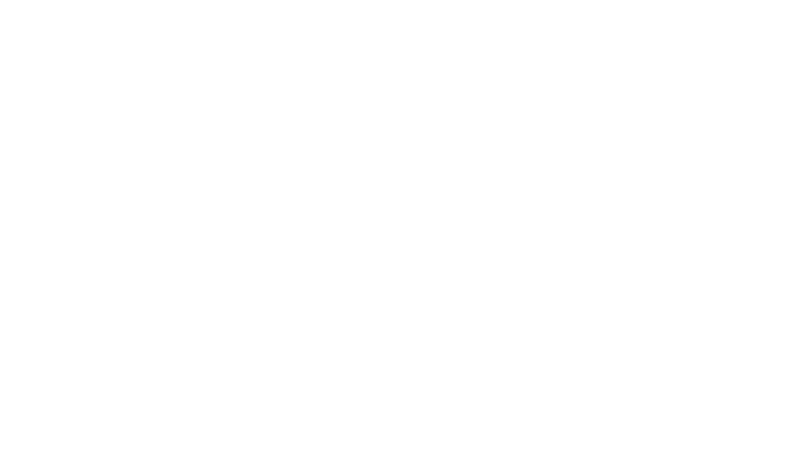
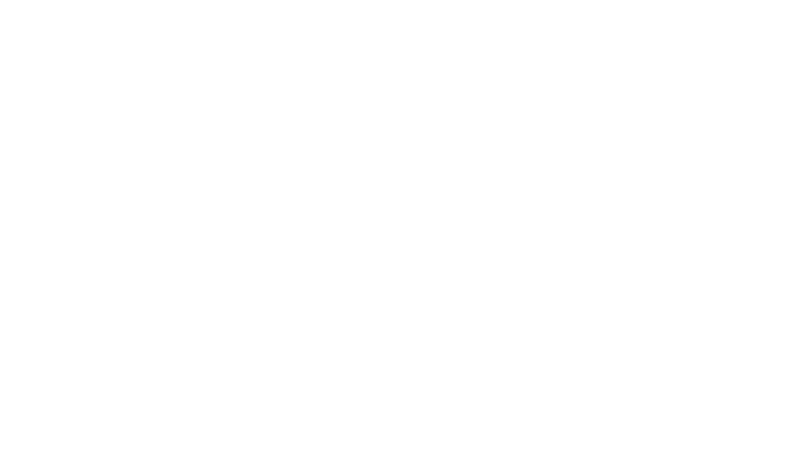
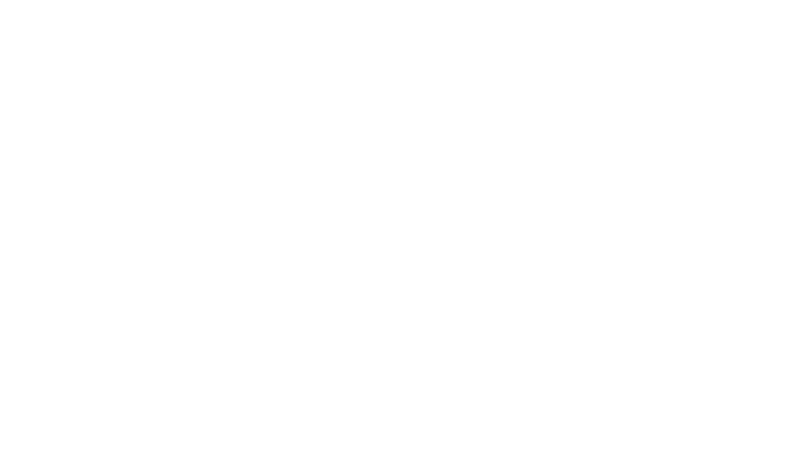
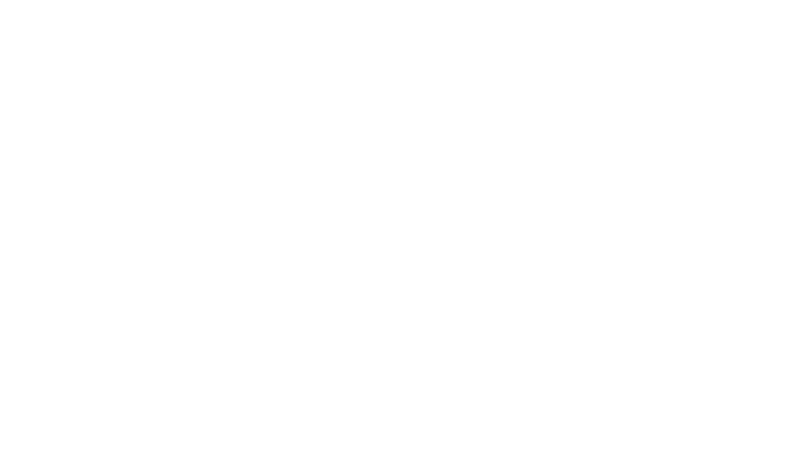
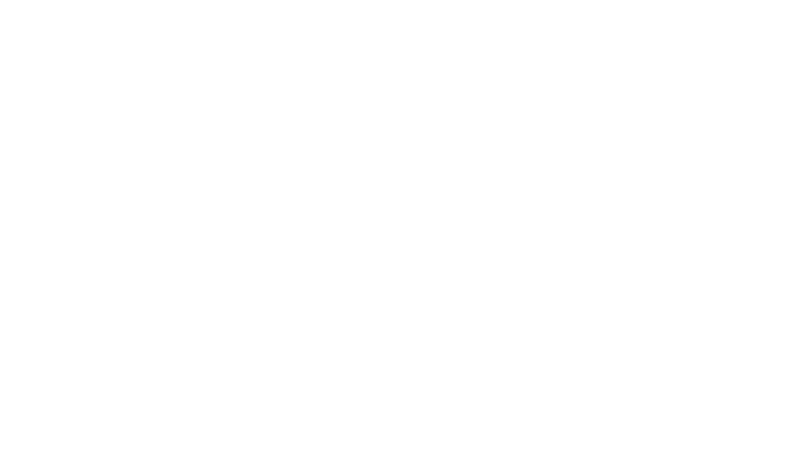