Hilton Hyde Park Central Dome - Remmers Ltd
Project
Hilton Hyde Park Central Dome
Product
Remmers MB PUReactive Plus
Size (M2)
100
Contractor
Building Transformation
Winner
LRWA Awards 2024
Liquid Roofing Project of the Year under 1000 sq. m.
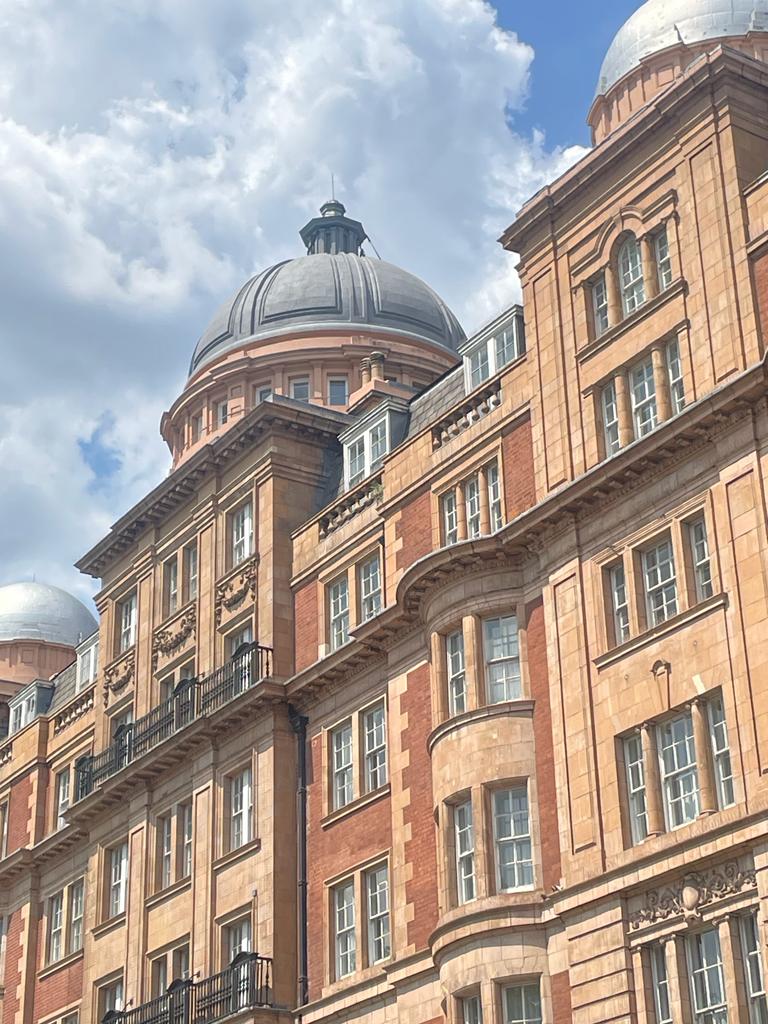
- The Background
One of the many iconic properties within their portfolio, the Hilton Hyde Park is a wonderful example of London’s architectural heritage, with enviable views directly across the park itself. With leaks causing damage to the main dome, a solution was needed to repair, re-coat and ensure the structure was sound.
As part of Building Transformations developing relationship with the Hilton brand, having worked with them across a range of requirements from façade and roof condition surveys, specialist leak detection and repair through to full façade and roof restoration projects across the UK, BT were initially asked to review a survey that had been provided by others and undertake the works required to the dome, which had been leaking for some time. The dome and the rooms within the hotel provide some of the best views across the city, so it was important that the leaks that had been identified were fixed so that once again this space could be utilised.
Working with this ideal in mind, BT were able to provide the client with a safe and successful approach that ensured all elements of the project were aligned with their specific needs, essentially repairing and re-coating the most difficult to access areas of the hotel, providing them with a long-term, minimal maintenance solution.
- The Solution
The Grade II listed property represents Edwardian splendour with a modern twist, ensuring the hotel is well maintained is key to the client’s objectives, as it is held with much historical significance and as a first class example of Edwardian architecture.
Built in 1907 and overlooking Hyde Park and Kensington gardens, it became part of the Hilton portfolio in 1999 and vitally retains many of its original features, including stained glass windows and roof.
Of the various domes across the roof, it was the main dome which was to become the focus for this project. With leaks having been a constant thorn in the hotel’s side affecting the main suite within the dome, a leak detection survey had been undertaken to identify the issues that were leading to the water ingress. Amongst these issues were cracked lead work, defects to the masonry including missing pointing and delaminated block work, rotten timber within the window frames, but chiefly the cracking and failure of the current coating system.
Working closely with the client to understand their initial and long-term goals for the property, BT with support from Remmers, were able to design, test and implement an access, product and delivery methodology that solved their problems, helping to protect the dome and reduce the need for maintaining this extremely difficult to access area.
The initial stage of the project saw further inspections and testing carried out, with the main 2 elements of this being the access and product choice. Remmer’s patented, MB PUReactive Hybrid Polyurethane waterproofing system was specified. Through adherence and crosshatch testing, Building Transformation & Remmers we were able to provide the client with a range of specialist products that would achieve their goal of waterproofing the dome, but also provide a warranty that aligned with their future needs.
As the project began, before it was possible for any works to be carried out it was essential that a crash-deck be put in place to cover the hotel’s entrance and the exit of the tube station next door. Through negotiations with the council, this allowed these areas to be protected and remain open, ensuring that the public below would not be affected.
It was then the turn of BT’s abseil, or perhaps in this instance we should call them their climbing teams to set up safe systems of work, as the dome sat atop the roof itself and would have to be climbed before work commenced.
Having tested the rigging system pre-project, BT knew that they could successfully mount an anchor point around the top of the dome which would allow their teams to work safely and freely across the entire area.
It was then down to them to remove the original coating, expose and repair the cracked and failed masonry beneath, then begin the meticulous and time consuming application of the specified Remmers MB PUReactive Plus waterproofing system, so that all areas of the dome were uniform. It was necessary to apply multiple coats and ultimately when finished, the Remmers MB PUReactive Plus waterproofing system was able to provide the client with piece of mind for the future.
Building Transformation work included
- Initial trials in conjunction with Remmers to ensure that the correct product was specified to provide the client’s desired level of cover, including cross-hatch and adherence tests, avoiding the potential for early failure and any future warranty issues.
- Due to the unique access requirements of working on this dome, which included aid climbing to the top of the dome and then abseiling down, the abseil team undertook access trials to ensure that safe methods of working could be put in place and rigging could be fully tested.
- The full removal of the current failed coating, stripping the system back to the masonry which then provided a sound surface to which the MB PUReactive Plus could adhere. This also involved extremely low impact methods to ensure that minimal dust was created and avoided the risk of this travelling on the winds that were present whilst working at height.
- Once the surfaces were fully prepared, any cracks or movement that had been identified were repaired and secured, again providing a sound surface for the Remmers system and also ensuring no areas were left where water could sit or penetrate.
- With the dome now fully prepared, the MB PUReactive Plus could be applied, this consisted of a multi-layered application of the Remmers patented, Hybrid polyurethane cold liquid applied waterproofing system, spread across all parts of the dome and built up to ensure water would not be allowed to penetrate the surface and a 10-year warranty could be achieved.
- With the timber window frames also being a source of leaks, these were rubbed back and repaired, any loose putty was removed and replaced, rotten timber was removed and then filled with a Remmers specialist timber repair care system, then all areas were re-coated with an external Remmers weathershield system to help protect against future weathering and minimise the need for ongoing maintenance.
- Where the windows were blocked up at the back, leading to condensation being present, weep holes were fitted to allow moisture to pass out of the void and ensure no further damage occurred.
- As was identified in the initial survey, the piece of lead that was damaged on the cupola at the top of the dome, was fully cleaned and prepared, then repaired and the crack sealed to ensure water could not ingress within that area.
- Gallery
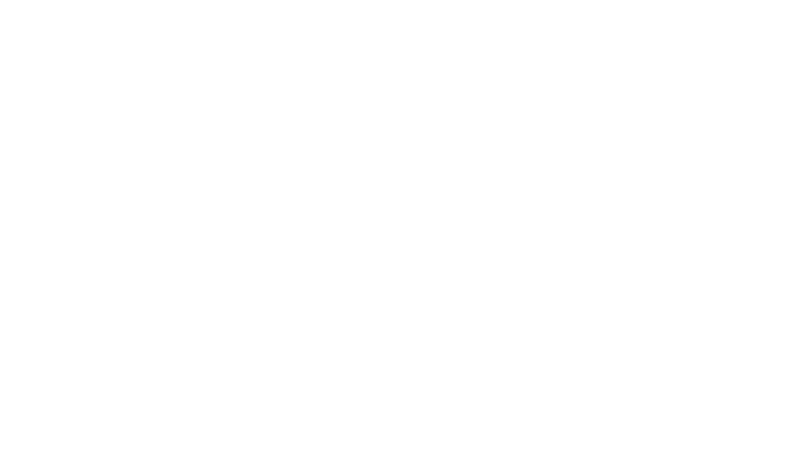
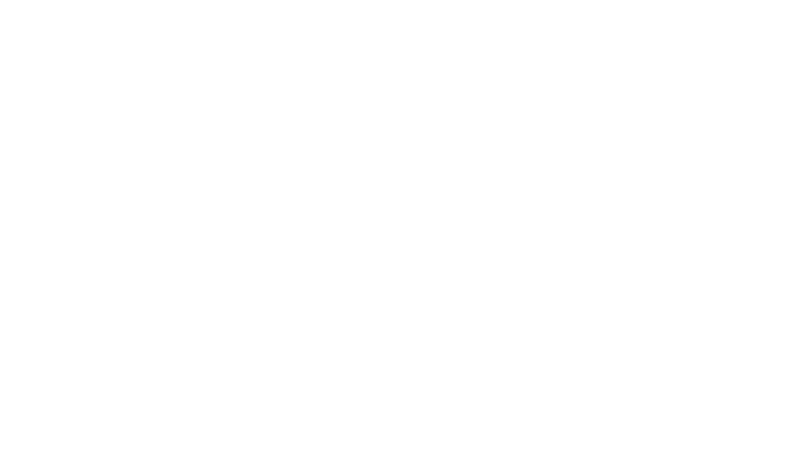
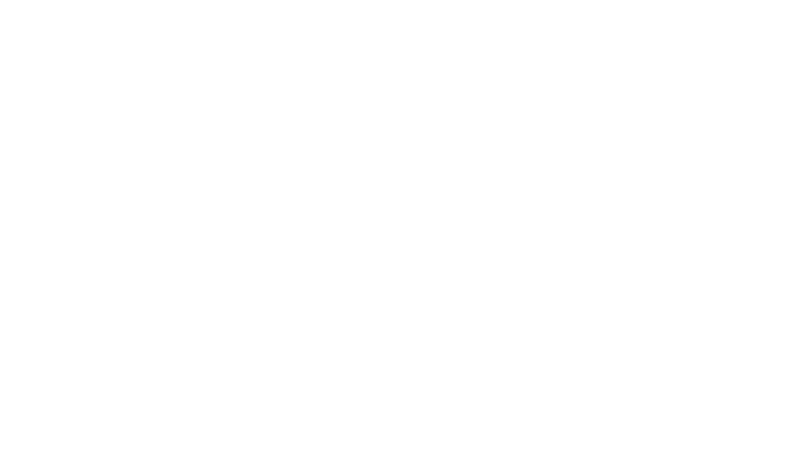
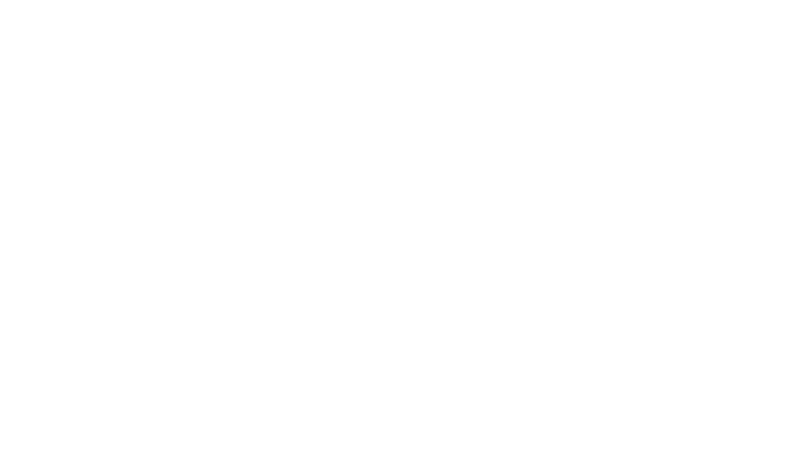
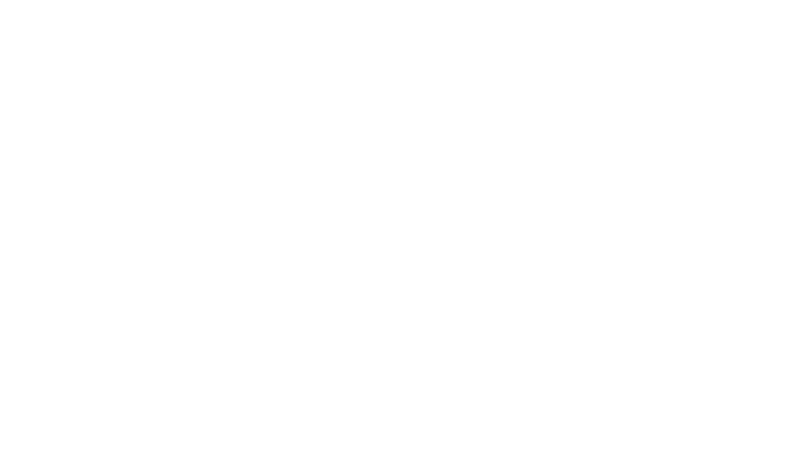
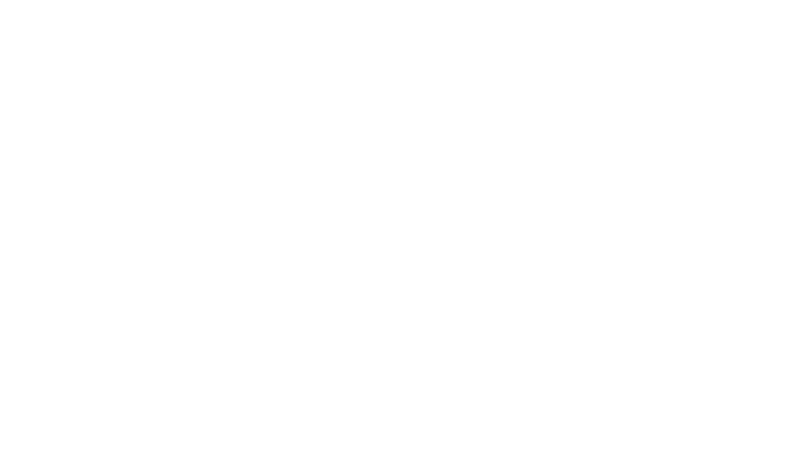
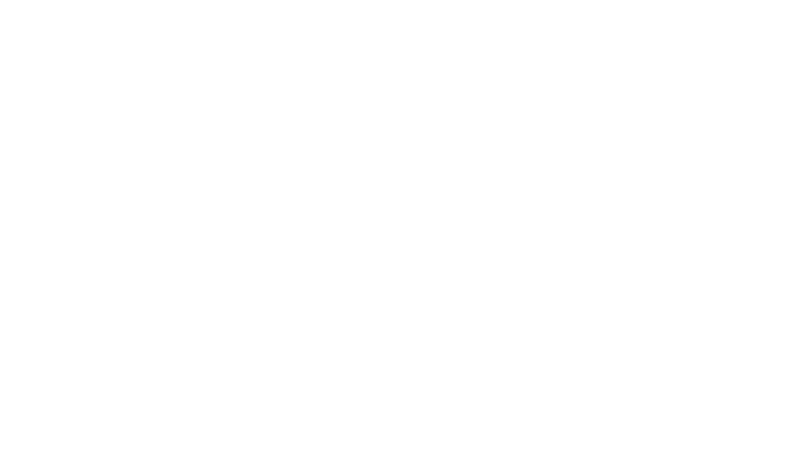