Host Helix Student Accommodation - Polyroof Products Ltd
Project
Host Helix Student Accommodation
Product
Polyroof Protec System
Size (M2)
1300m2
Contractor
Tower Asphalt Ltd
Winner
LRWA Awards 2023
Liquid Roofing Project Over 1000m2
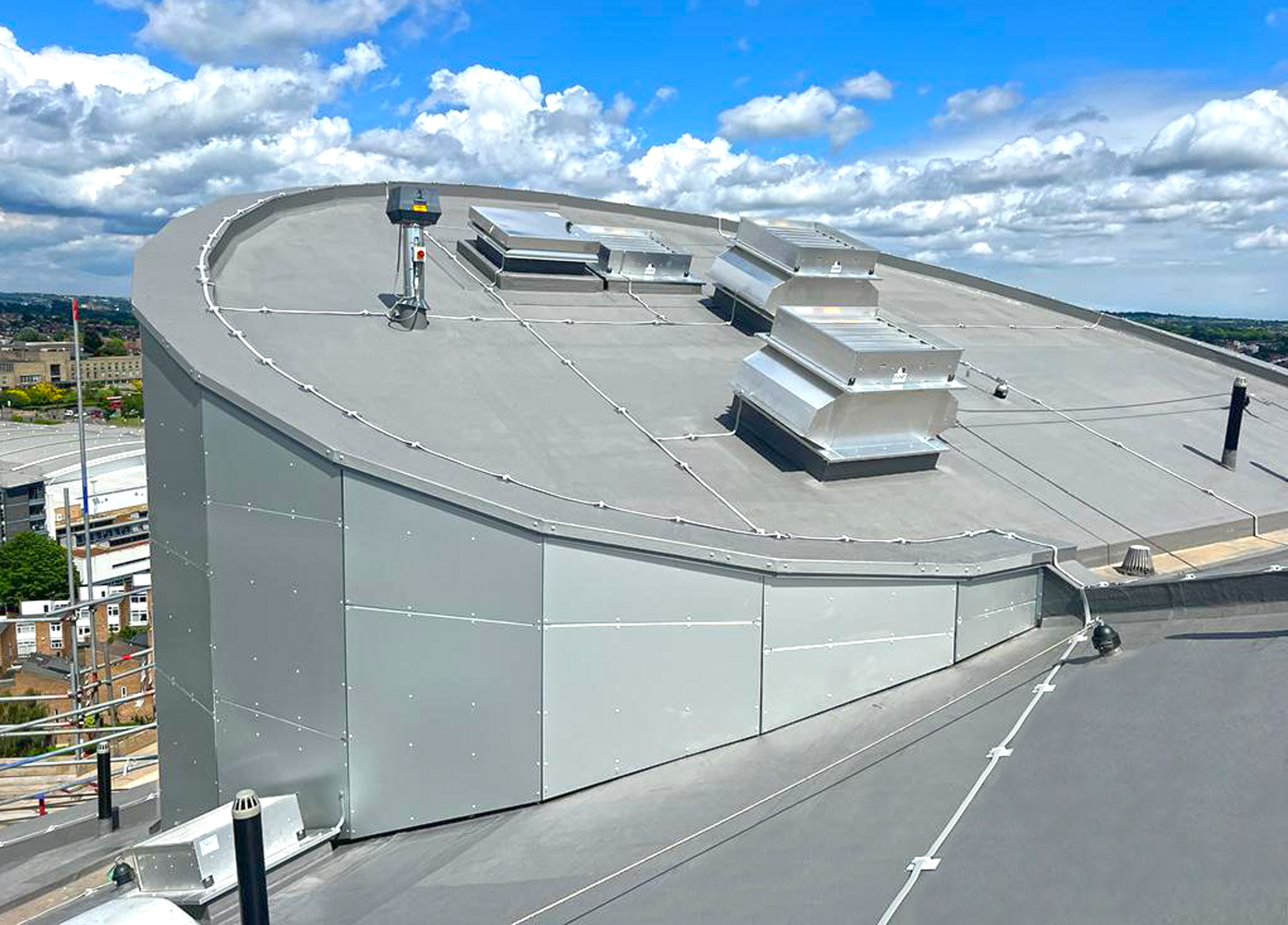
- The Background
With stunning views across North London and Wembley Stadium, a curved and pitched building like nothing we have ever seen before, Host Helix was a project to remember. Nicknamed the “Helter-Skelter”, Host Helix was built in 2011 ready to host athletes in the 2012 Olympic Games. The building since has been used as a university hall of residence before closing this year for refurbishment. After general wear and tear over a ten-year period, water began to enter the building due to the complexity of the building shape, guttering and vast amount of plant on the roof. Polyroof Products were requested to consult with the clients to offer a seamless, encapsulated solution that could address the many unusual details associated with this unique building design.
- The Challenge
A full survey of the roof terrace areas was carried outby the Polyroof Technical Services, after which a bespoke specification was produced for the works. Within minutes of the survey beginning, it could be seen that the complex and winding curves of the building would be one of the most complex and unusual projects ever completed by both Polyroof Products Ltd and Tower Asphalt Ltd. The proposal document detailed a comprehensive set of recommendations for producing a seamless solution to encapsulate the problematic roof, therefore solving the issues that had arisen over the years due to its condition and age, as well as the issues associated with the original design of the pitched, curved roof. The client was satisfied that the solution proposed for the refurbishment would provide the lasting peace of mind they were looking.
- The Solution
The contract was awarded to Polyroof Products Ltd and Tower Asphalt Ltd to overlay the existing single ply membrane with the Polyroof Protec System. Such an iconic building in the local community, the client wanted to leave no stone unturned. Therefore, the Protec system installed at the perimeters was colour matched to the university colours, namely the blue and grey cladding on the exterior of the building, so that once installed it was not visible from the ground. This was achieved by blending a range of pigments until they replicated the desired colours which in turn was blended into the Protec resin prior to application. From the survey, concerns had also been raised regarding the original building designs from 2011 and the drainage system on the roof. Due to the pitch of the roof, rainwater had been cascading down the curved slopes at some velocity and bouncing up under the original capping resulting in water ingress into the building. Following numerous discussions between the main contractor and Polyroof, in conjunction with the provider of the external cladding, it was agreed that the perimeter detail needed to be encapsulated with the new waterproofing system. This would help avoid further water ingress into the building via the perimeter edges under the cappings. To encapsulate the building edges, fire-retardant cement particle boards were fixed to the internal and top faces of the external parapet walls. Polyroof SA Carrier Layer was then applied over the cement particle boards with Polyroof pre-formed GRP Drip Trims fixed to the external edge. The Protec System was applied to encapsulate the entire parapet detail. This process was more complicated further by the curvature of the building. Polyroof pre-formed GRP Drip Trims are 2.44lm in length. The contractor took a lot of time and patience carefully cutting the trims to size prior to fixing to the external edge to ensure they followed the profile of the structure. In addition, due to the height of the building, all the trims were face fixed to avoid any wind uplift concerns.
To further help with drainage away from the hotspot areas of the roof, the contractors were asked to create new internal curved gutter channels at the interface between the building and roof. This would provide sufficient upstand height and help direct any rainwater towards the outlets. This process was again complicated because of the curvature of the building. Due to the pitch and curvature of the roof, health and safety was more critical for the contractors working on site than it would usually be working on a standard flat roof. Further measures were taken such as the use of mansafe and additional curved scaffolding systems to ensure work safety(Image 4). The works were completed to an extremely high standard with full encapsulation of the curved roof areas and without a single detail being left exposed to the elements. Following completion and Polyroof’s final inspection, the client was extremely pleased with the service and product they received
- Gallery
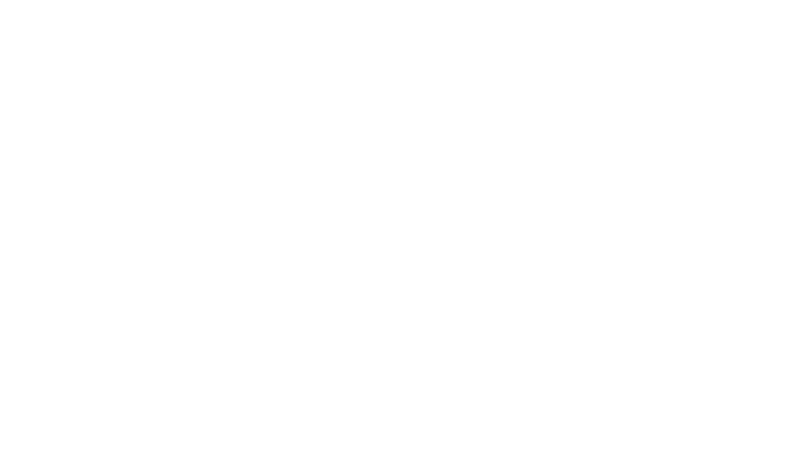
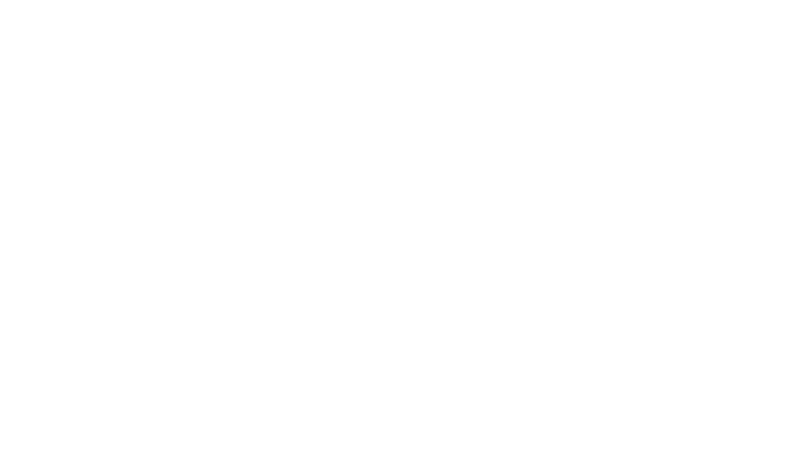
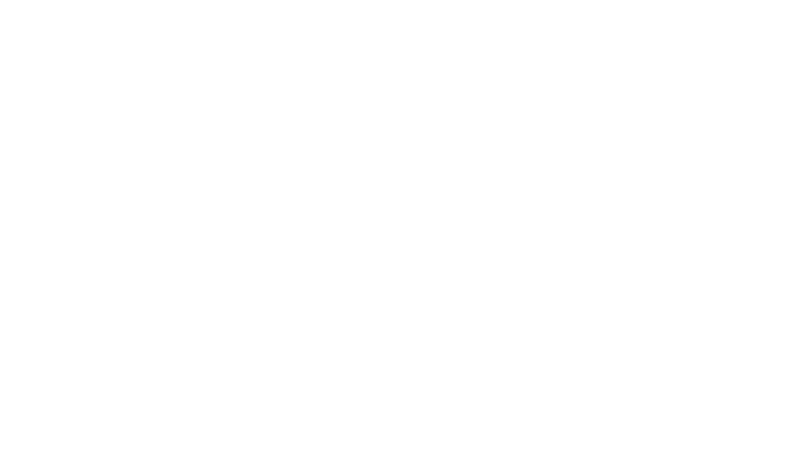
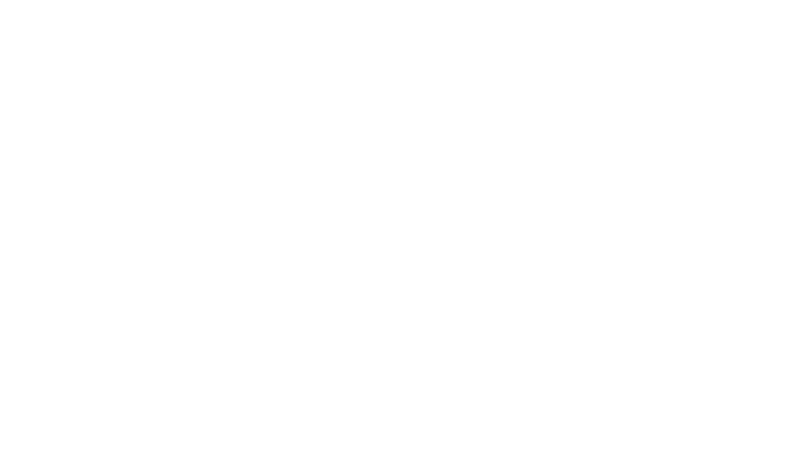