Main Stand, Cheltenham Racecourse - Makers Construction Ltd
Project
Main Stand, Cheltenham Racecourse
Product
Polyroof Protec
Size (M2)
2300m2
Contractor
Makers Construction Ltd
Winner
LRWA Awards 2023 - Highly Commended
Liquid Roofing Project Over 1000m2
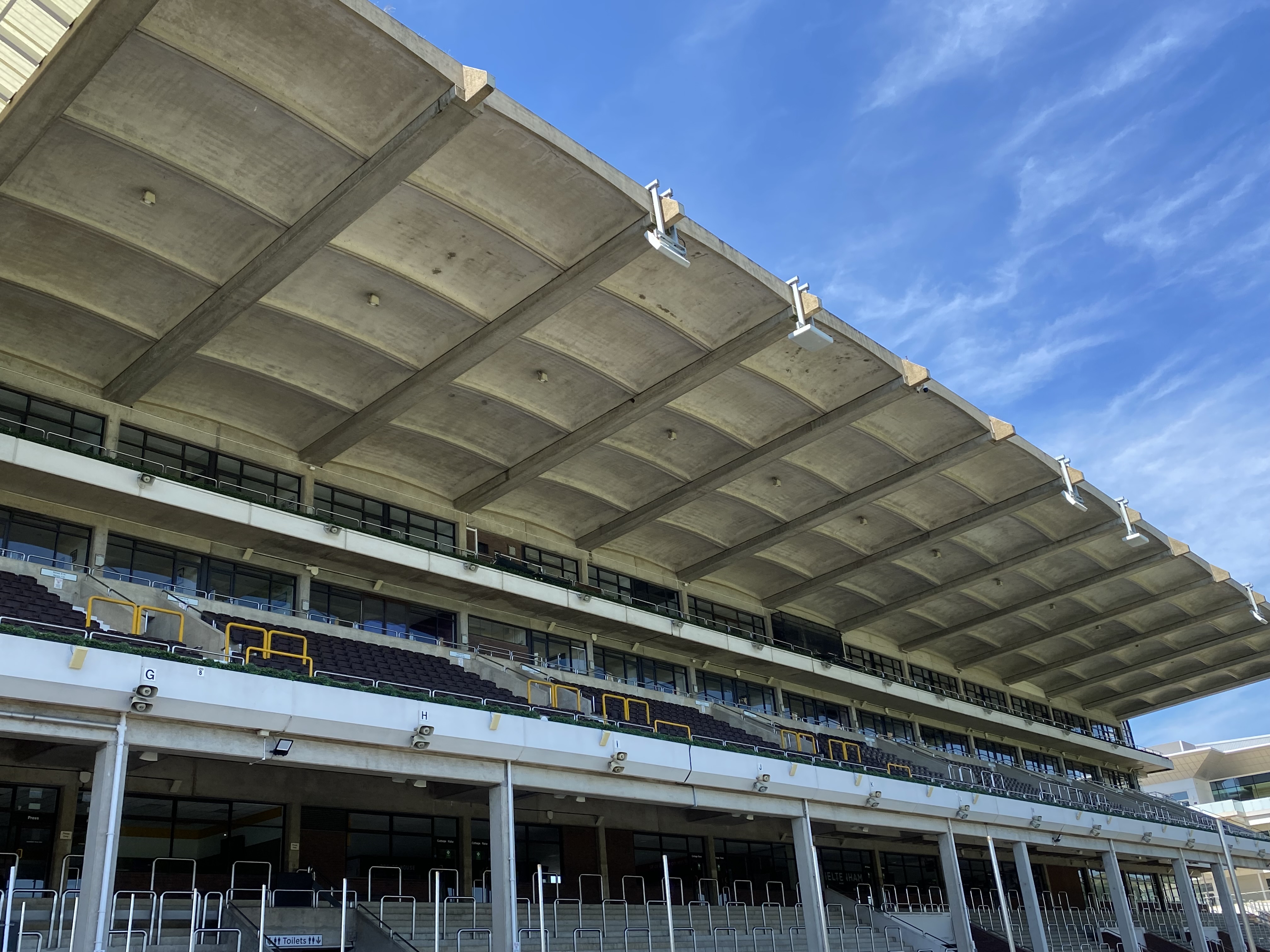
- The Background
Home of arguably the greatest flat horse racing event in the world, Cheltenham Racecourse is set in a scenic location in a natural amphitheatre, just below the escarpment of the Cotswold Hills at Cleeve Hill. The Jockey Club engaged Makers Construction to carry out a survey on the Main Stand Roof. The unique cantilevered reinforced concrete barrel roofs had visible signs of water ingress due to existing coatings failing allowing water to penetrate and to corrode the steel. There were also issues with water ingress into the buildings and on to the punters below. Makers engaged Polyroof Products to carry out testing and produce a specification for the project. Polyroofs Protec flexible hybrid polymer was the selected product to carry out this 2300m2 overlay project.
- The Challenge
There were many difficulties and challenges regarding this project. Due to the location of this roof, height 18 -20 m and the ongoing use of the conference facilities an external access tower wasn’t an option for the client. A designated internal access route was devised for the delivery team with full protection to all surfaces and lifts. Makers engaged a crane company to lift all materials on to the roof in one hit, therefore accurate measures were taken to ensure all materials were ordered and onsite. Once the works were complete the waste was then craned to ground level.
The existing coating had failed in many places, this required stripping back by mechanical means to get back to a sound surface that was ready to coat.
Due to the barrel of the roof the perimeter gutters running parallel were extremely difficult to access and required the operatives to lie down to coat the gutter bases.
Each section of roof has its own large concrete upstand that divides each roof. These upstands have indentations and column sections which made it extremely difficult to detail and was a slow process.
Makers had to plan around race events to make sure work areas were completed to a watertight standard before pulling off site.
Each barrel section of roof (65 in total) has an expansion joint, Makers and Polyroof had to come up with an effective detail for each of these joints to ensure continuous waterproofing.
The upstand to the external edge had a number of failing concrete areas. We highlighted these as an area of concern and repaired as part of the water proofing system.
This roof is heavily used for camera equipment during the main race meetings. The team had to carry out intricate area of detailing around the steel work that the cameras sit on. There is also a large amount of thick armoured cabling that was sitting in gutters and on parapets that had to be lifted and worked around.
Due to the roof being made up of 65 barrels joined together the operatives had to work methodically and carefully as the liquid had a tendency to run and slump down the curves if applied too thickly.
Finally, Cheltenham Racecourse sits at the foot of the Cotswold Hills. this creates its own microclimate and in Autumn has a high level of rainfall. This had to be managed and forward planned by the Makers team to ensure no coatings were damaged. In total approx 30 days were lost to the weather.
- Gallery
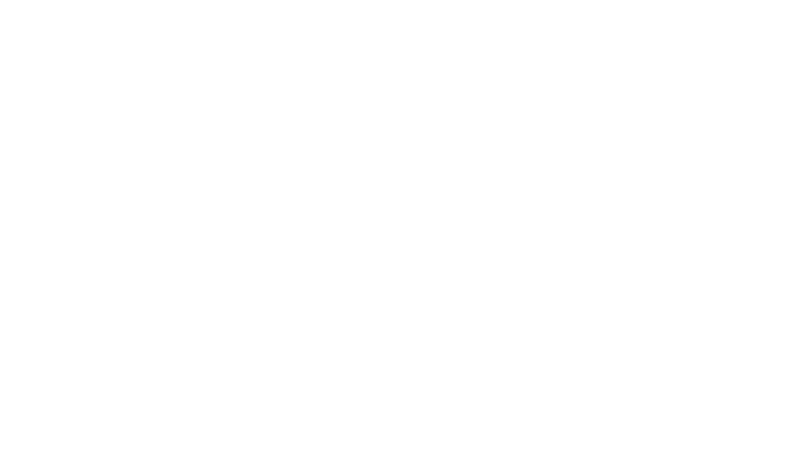
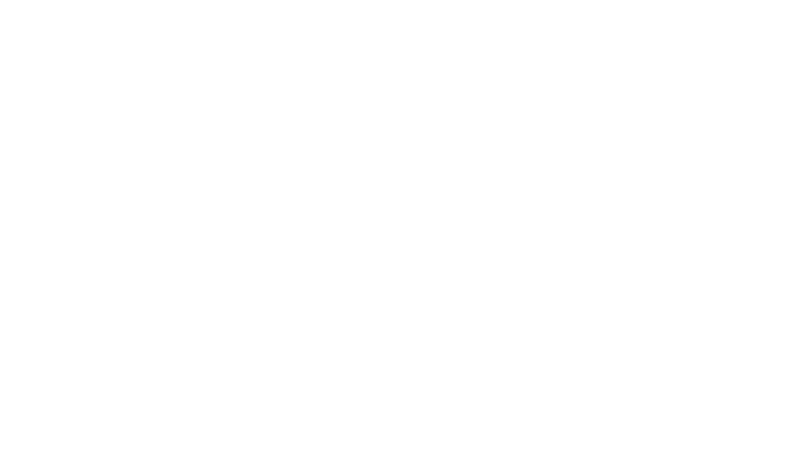
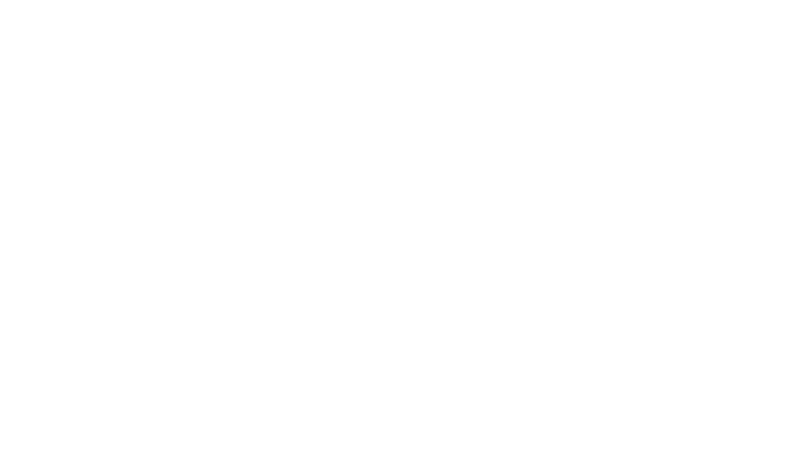
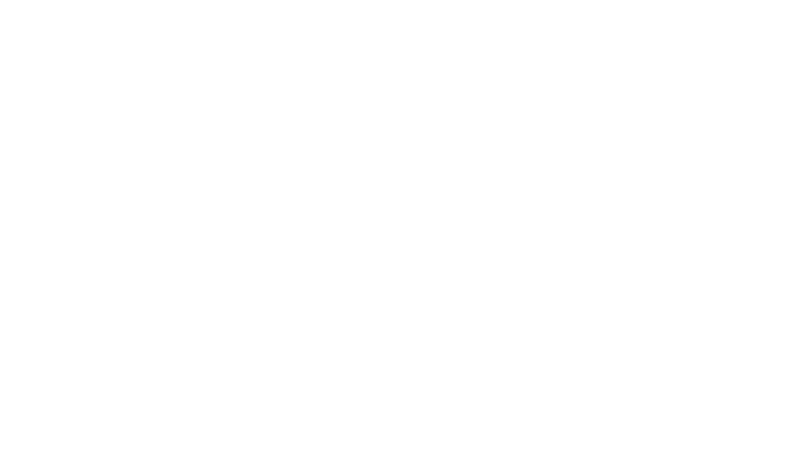
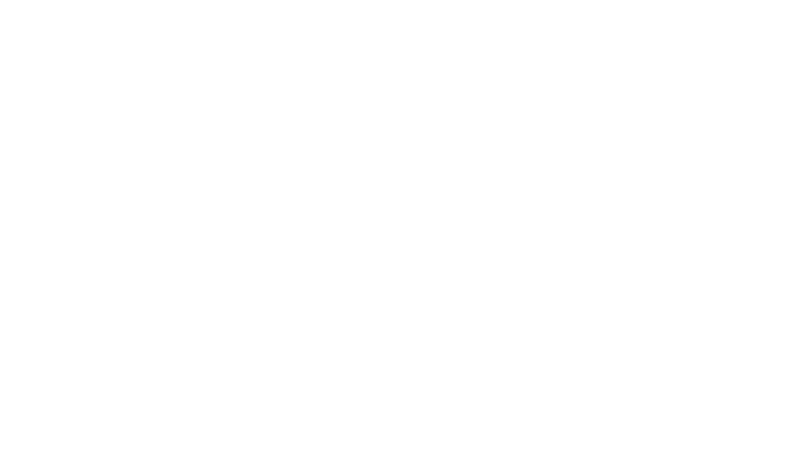
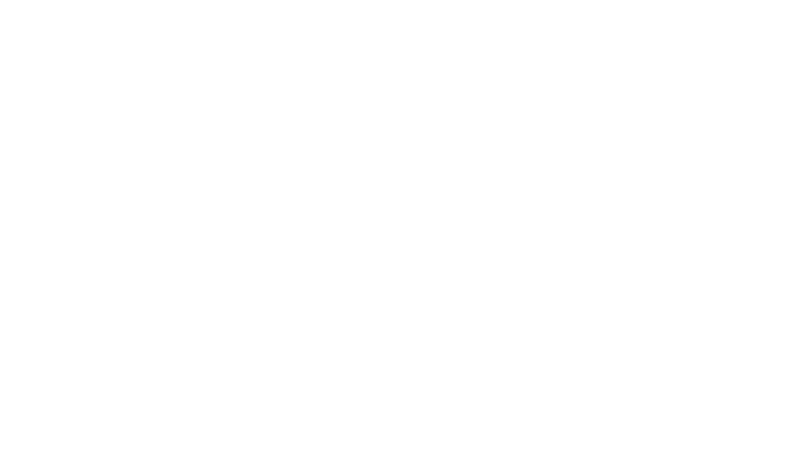
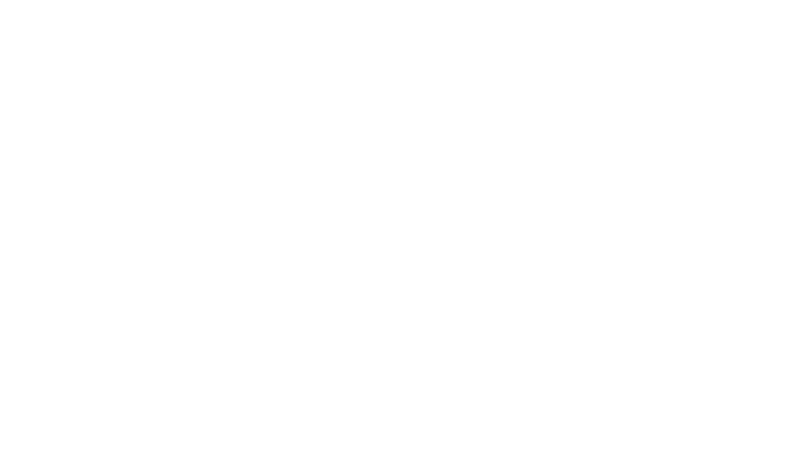
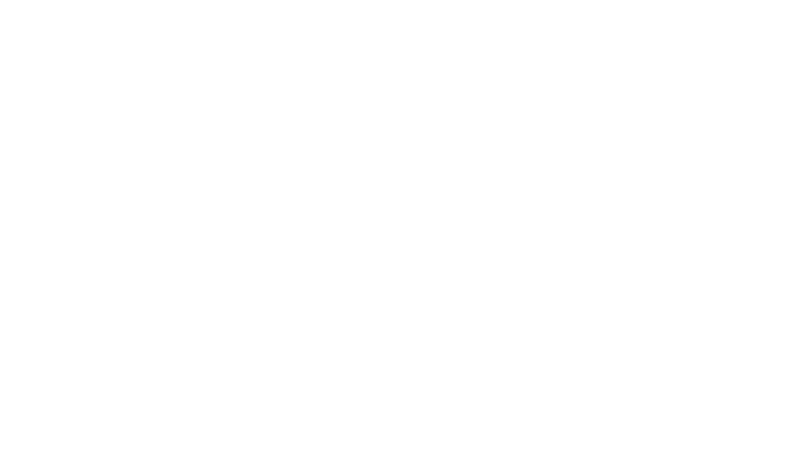
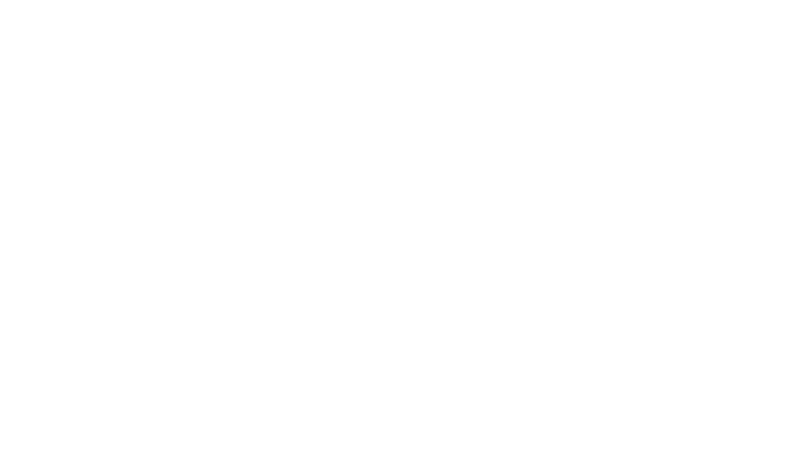