Old Bailey - Westwood Liquid Technologies Ltd
Project
Old Bailey
Product
Wecryl 230
Size (M2)
800
Contractor
Ifield & Barrett Roofing
Winner
Highly Commended LRWA Awards 2024
Liquid Roofing Project of the Year in a Buried Application
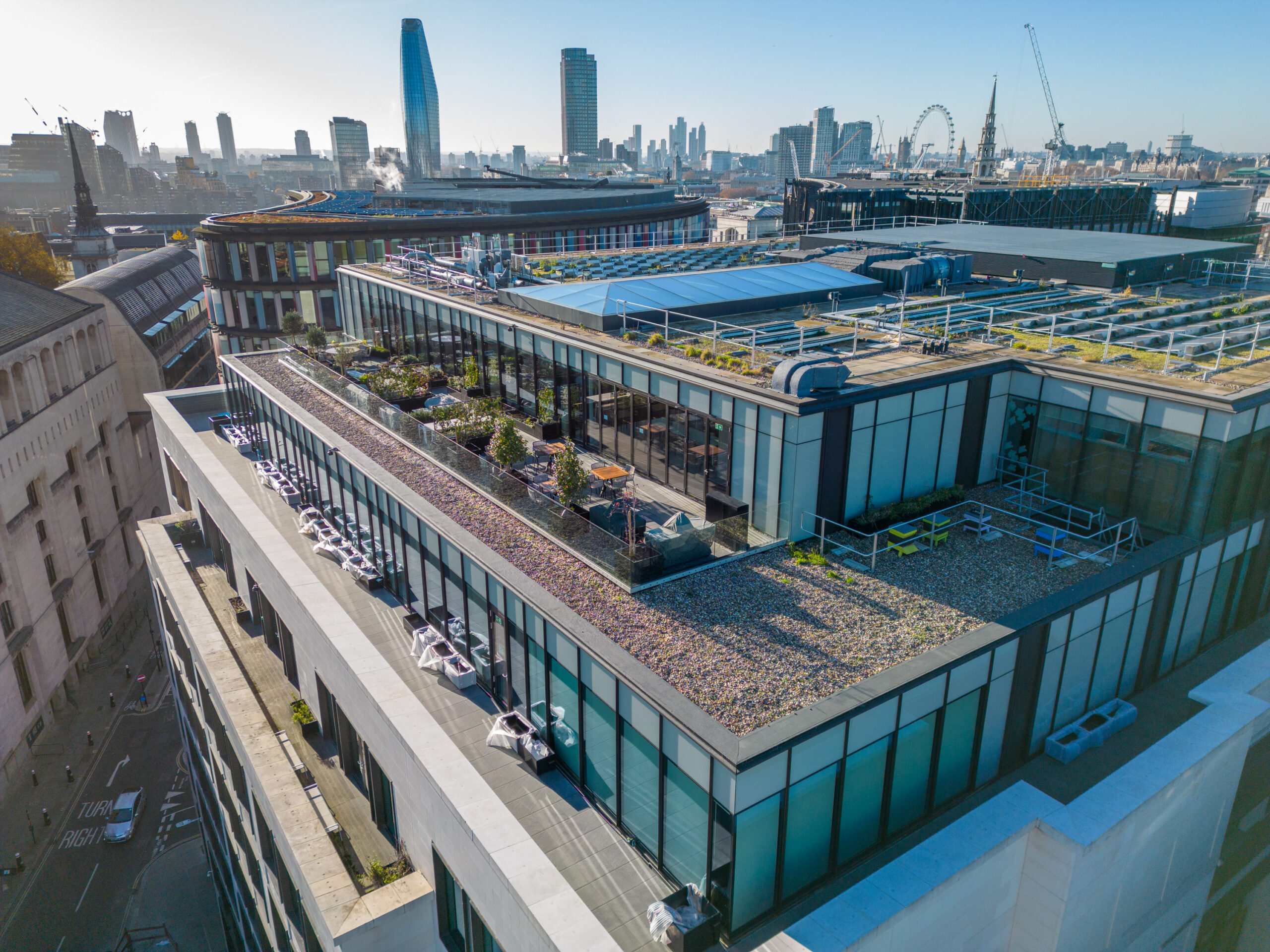
- The Background
WestWood’s innovative and durable solution offered outdoor communal space for a high-end, thriving office building in the centre of London.
WestWood Liquid Technologies designed a new terrace provision to replace original materials that were not performing effectively. Water ingress was therefore impacting the occupiers and tenants in the floors below.
- The Solution
A waterproofing challenge of this complexity could not be met by conventional roofing contractors, but operatives with experience working on the tower. Specialist roofing and general contractors, Orb Rope Access Ltd, were chosen as they had previous knowledge of the building, working at extreme heights, and are Proteus Approved contractors trained in the use of our Cold applied liquid systems.
The existing waterproofing was a liquid system applied over foam glass insulation onto the concrete structure of the building. Completely stripping the entire roof area would have provided extreme challenges and danger to the contractor, building occupants and public below. Following extensive surveying, Proteus established that they were able to work with the existing substrate after repairing and removing significantly damaged and wet areas only. This further helped to reduce material usage while providing a positive impact for both the environment and the contractors safety.
This incredibly unique project possessed many design and installation challenges. To meet the client’s requirements of a fully repaired and resilient waterproofing system and prevent the insulation being crushed again, a protective timber upstand ring was designed, made at roof level, and installed to the top of the rood edge detail. Individual bespoke pieces of plywood had to be measured, cut, and bonded to fit the undulating vertical face above the windows, and another piece bonded around the perimeter of the domed circular roof to form a firm corner where previous damage had occurred. Once the ply was cut, that exact piece had to be taken to the correct location around the edge of the roof and bonded into place before the Pro-Prime® SA and Pro-Vapour Control/Carrier Membrane SA could be applied. Proteus Pro-System® was overlayed to provide the ultimate watertight protection.
Once the perimeter detail had been constructed, the roof area was jet washed. Pro Epoxy Primer was applied to the existing window cleaning rail and outlets to allow the smooth application of Proteus Pro-System®. The entire roof area could then be primed with Pro-Reactivation Primer, followed by the Proteus-Pro-System® Reinforced system providing the client with seamless, robust, and aesthetically pleasing waterproofing protection guaranteed for 20 years.
Applying waterproofing at such height comes with an abundance of challenges. Weather conditions substantially differ at height, making wind and rain speed incredibly intense. Wind proved to be the greatest challenge as although it felt mild at ground level, the higher the operatives climbed, the more forceful it became. This was especially prevalent when applying the carrier membrane and fibre glass as the wind kept blowing the sheets and matting making application incredibly problematic.
Being such a tall structure, the tower naturally sways in windier weather further adding to the challenges. As well as securely harnessing themselves to the building, the contractors had to ensure all tools and products were also firmly secure to avoid any items falling from the roof. These were clipped to the operatives’ harnesses as they were dangling over the edge 130m in the air making waterproofing application, and movement around the roof perimeter incredibly difficult.
The rain also bought significant difficulties to the operatives. The roof perimeter became very slippery in wetter weather conditions, making access to the roof incredibly dangerous. Operative safety is always at the forefront of importance, meaning on several occasions works could not be completed, causing delays in the progress of works.
Proteus Pro-System® was the perfect waterproofing solution for this incredibly complex project. Due to the significant height of the building, it is structurally designed to move to alleviate wind pressure and avoid cracking. The strength of Proteus Pro-System®, paired with the fibre glass matting, will allow for the natural movement of the building without causing any damage to the membrane.
As well as standing at great height, the Radio City Tower is iconic for its unique ‘flying saucer’ shape. Proteus Pro-System® was the ideal liquid solution for its ease of application on this unique structure, especially for the intricate detailing around the window cleaning rail and metal plinths.
Avoiding the risk of fire is always of utmost importance. As Proteus Pro-System® is cold installed, it complies to the projects Health and Safety criteria, while completely eliminating the risk of fire. All works could be completed while the building was in use meaning the radio stations could operate as usual with minimal disruption.
Orb Rope Access Ltd have a wealth of experience working at height and using waterproofing materials. They received additional training at our facility in Barnsley to refine their skills and build confidence in using Proteus’ systems. They were supported throughout the application by a member of Proteus’ technical services department to inspect the progress of the works and offer advice on products and application if required.
Collaboratively, Proteus Waterproofing Ltd and ORB Rope Access Ltd successfully delivered this project to an impeccable standard resulting in one incredibly satisfied client, and an iconic skyscraper fully waterproofed for many years to come.
Proteus Waterproofing Ltd only supplies products to contractors whose operatives are of a suitable skill level and have demonstrated their competence at our product training events. Installation guidance, product datasheets and material safety datasheets are provided to all contractors who have attended these programmes and, as a result, been issued with a Proteus Approved Installer card. Throughout the project installation, Proteus’ technical services attended site to inspect the progress of the works and offer advice on products and application if required.
- Gallery
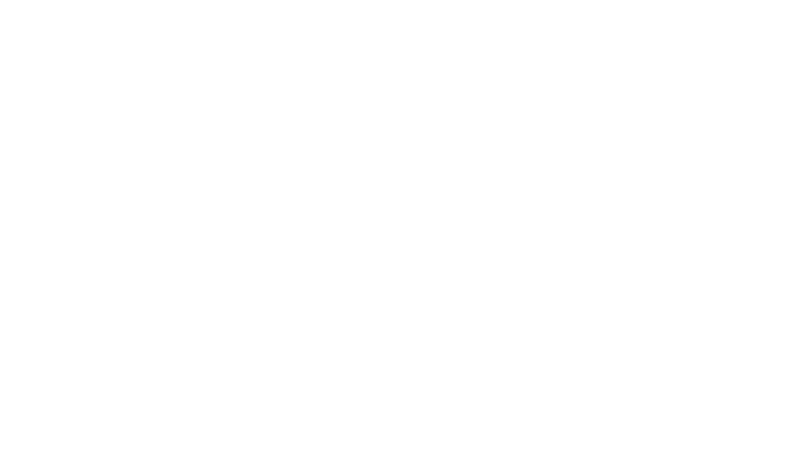
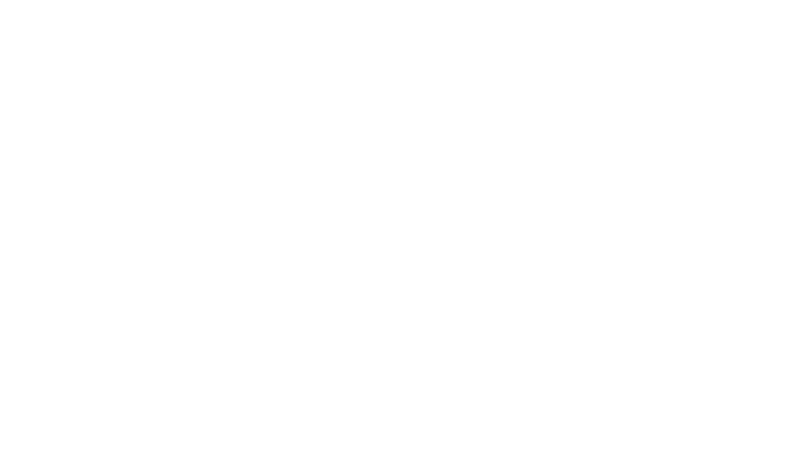
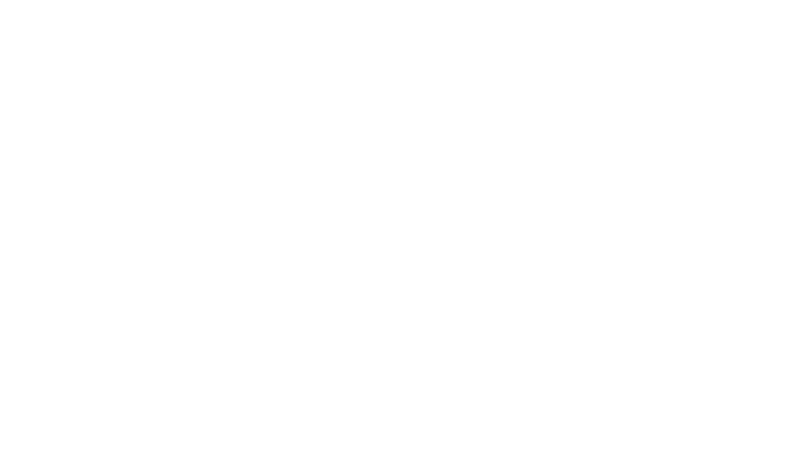
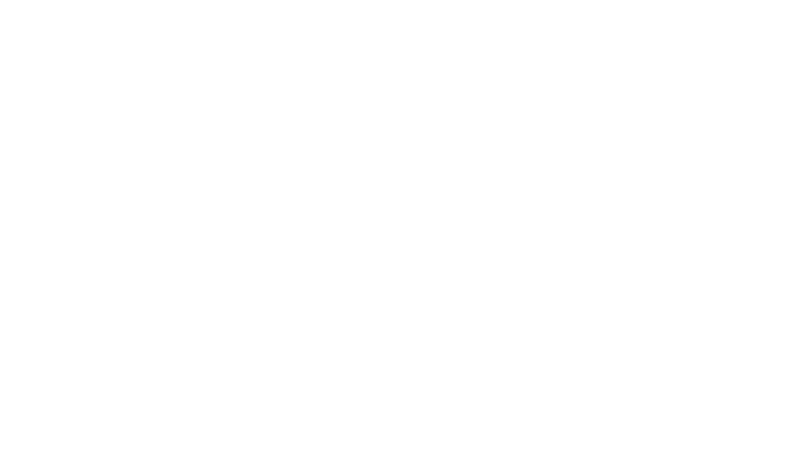
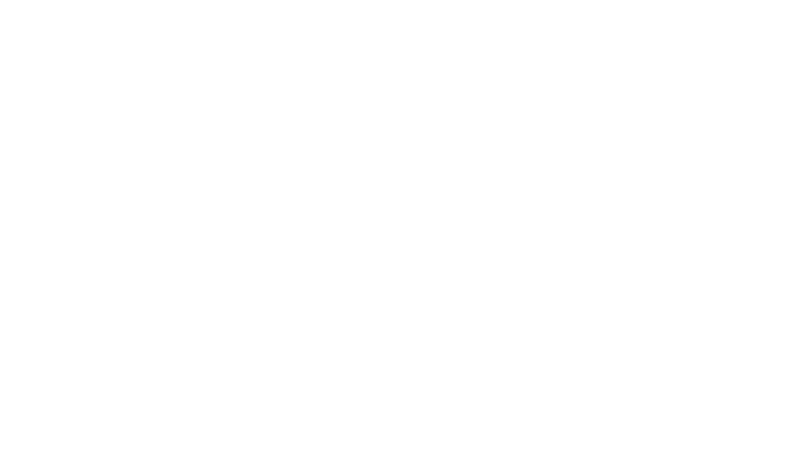
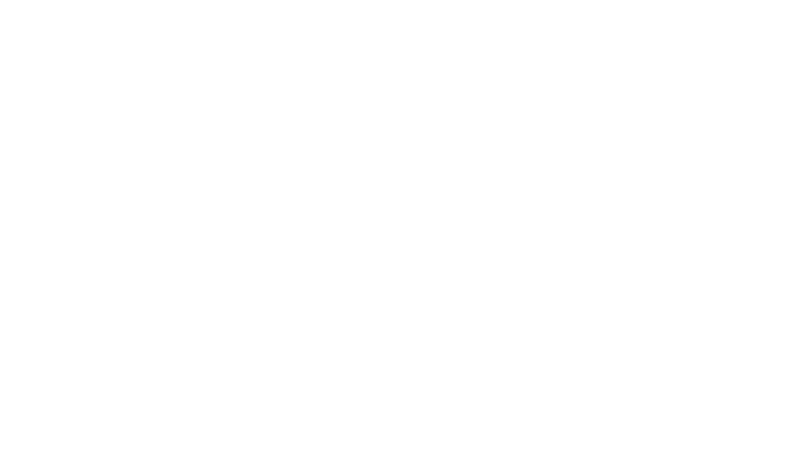
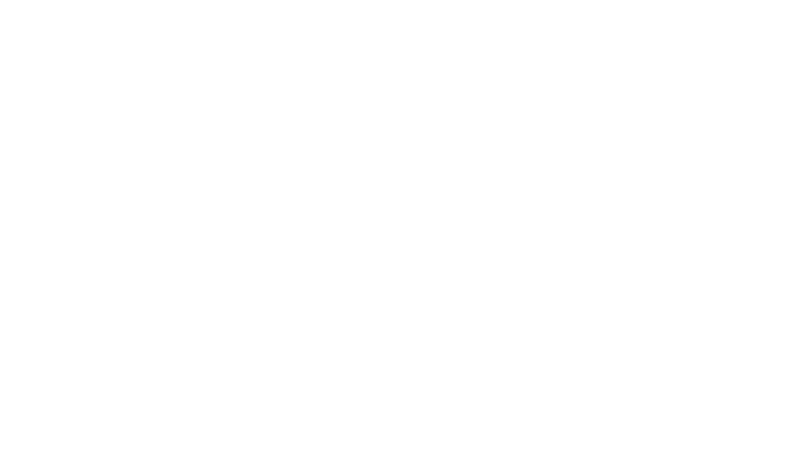